Introduction
What is a lithium battery pack?
Battery pack generally refers to the com battery, which mainly refers to the processing and assembly of lithium battery sets. It mainly processes cells, battery protection panels, battery connectors, label paper, etc. into products needed by customers through the battery pack process combi. At present, the battery pack is mainly concentrated in the lithium battery bag pack factory. It all has its own pack structure design, pack electronic design, and pack production workshop. It can carry out independent development and design according to customer needs, and achieve customer pack through battery solutions, battery specifications, and battery samples. After the customized requirements of lithium batteries are confirmed, the pack production line of the packing workshop will be produced and processed, and the goods will be shipped after passing the quality inspection.
Lithium battery monomer, lithium battery, and lithium battery pack?
- Lithium battery monomer: the most basic element that constitutes the battery pack and the battery bag, and the voltage generally provided is between 3v-4v;
- Lithium batteries: composed of multiple monomers to form a single physical module, providing higher voltage and capacity;
- Lithium battery packs (packs): They are generally made up of multiple battery packs, and battery management systems (BMS) are added, which are the products finally provided to users by the battery factory. That’s what people often call lithium batteries.
Pack Composition:
Pack includes battery packs, confluence, soft connections, protective panels, outer packaging, output (including connectors), highland barley paper, plastic brackets, and other auxiliary materials to form the Pack.
- Pack:
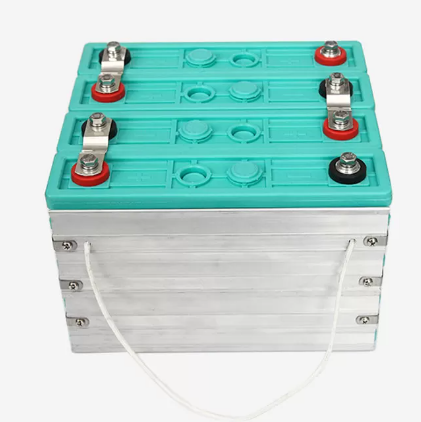
- Battery packages require a high level of consistency (capacity, internal resistance, voltage, discharge curve, Life).
- The cycle life of the battery pack is lower than that of a single battery.
- Use under limited conditions (including charging, discharge current, charging mode, temperature, etc.)
- After the lithium battery pack is formed, the battery voltage and capacity are greatly improved, and it must be protected, and its charging balance, temperature, voltage, and overcurrent monitoring.
- The battery pack must meet the voltage and capacity requirements required for design.
- Pack Method:
- String and composition: The battery is composed of a monomer battery and connected in series. The capacity is increased in parallel, the voltage remains unchanged, the voltage is doubled after series, and the capacity remains unchanged. For example, the 3.6V/10Ah battery consists of a single N18650/2Ah through 5. Parallel string: Parallel connection will affect the battery cycle life after parallel due to differences in internal resistance and uneven heat dissipation. However, a single battery failure will automatically exit. In addition to the reduced capacity, it does not affect the use after parallel, and the parallel process is strict. When a unit battery in parallel is short-circuited, the parallel circuit current is very large, which is usually avoided by fuse protection technology.
First string and then: According to the battery capacity of the whole set, it is connected in series first, such as 1/3 of the whole battery capacity, and finally connected in parallel, which reduces the probability of large-capacity battery failure.
- Cell requirements: Select the corresponding cells according to your own design requirements. The types of batteries in parallel and series are the same, the models are the same, and the difference in capacity, internal resistance, and voltage values is not more than 2%. Generally speaking, after the battery is combined in parallel series, the capacity will lose 2% to 5%. The more batteries there are, the more capacity will be lost. Whether it is a soft package battery or a cylindrical battery, multiple combinations are required. If the consistency is poor, it will affect the battery capacity. The lowest capacity in one group determines the capacity of the whole battery. High current discharge performance is required. The starting current of the motor is three times that of the normal current, and high current discharge can improve the power performance of the motor. Requires good battery cooling. The number of batteries is large, and the rise in the battery temperature inside the battery box is not easy to disperse, resulting in uneven temperatures between batteries, different discharge characteristics, and long-term degradation of battery performance. The production process level is high. The battery should be able to withstand the vibration impact of bumpy roads. It has high requirements for the production process, especially the spot-welding process. After welding, it is tested to prevent virtual welding and de-welding.
Buy Now: Semco Infratech – SI Battery Charge & Discharge Cabinet Tester – SI BCDS 100V 20A 4CH.
- Process of 3 pack-
- The pack of the battery is realized in two ways. One is through laser welding or ultrasonic welding or pulse welding. This is a common welding method. The advantage is that it is reliable but not easy to replace. Second, it is contacted through elastic metal sheets. The advantage is that it does not need welding, and the battery is easy to replace. The disadvantage is that it may lead to poor contact.
- Charge and discharge time –
Charging time (hours) = (battery capacity Ah x charging coefficient) / charging current A
Discharge magnification: The discharge magnification of the battery is expressed by the discharge time or hourly coefficient required to discharge the rated capacity of a certain discharge current. Among them, discharge magnification = rated capacity/discharge current.
In the packing process, such as nickel sheets, copper-aluminum composite juice, copper bolts, totally positive and total negative bolts, and aluminum bulbs will also be used. Copper soft connections aluminum soft connections, copper foil soft connectivity, etc. The processing quality of confluence and soft connections needs to be evaluated from these aspects.
- Whether the material meets the requirements, and the failure of the confluent material will increase the resistivity. In particular, it is necessary to confirm whether it meets the relevant requirements of ROHS.
- Whether the key size processing is in place. The excess of key dimensions may lead to insufficient safe distance between high-voltage devices during assembly and serious safety hazards.
- The binding force of the soft connection hard zone and the stress absorption of the soft area.
- Whether the overcurrent capacity of the actual processed soft connection and the confluence row meets the design standard, and whether the insulated thermoplastic casing part is damaged.
- Six factors to consider in the structural design of a pack of lithium battery packs:
- Lithium battery package structure pack design involves many levels:
For example – In mechanical structure design, we should consider strength, shock resistance, heat dissipation, waterproof, dust prevention, etc.,
electrical design, security regulations, EMC security regulations, etc. we should also consider the design of lithium battery management systems, including overshoot, extension and extenuation estimation. Detection accuracy, battery balance, etc., to ensure the safety and reliability of the battery must be reasonably designed and confirmed by the market.
Buy Now: Semco Infratech – SI Battery Management System Tester – SI BMST 1-32S 60/120A with cabinet.
- Factors to consider in the structural design of a pack of power lithium batteries –
- Waterproof, waterproof rating up to IP68;
- Maintain the air pressure balance inside and outside the lithium battery pack, because the temperature of the battery pack will change during charging and discharging, which leads to a change in the air pressure in the battery pack, and the PUW explosion-proof valve can breathe without leaking water, so it can keep the air pressure inside the bag same as the outside world.
- Explosion-proof: Once the lithium battery pack is thermally out of control, the air pressure in the battery pack rises sharply. At this time, the battery pack is in danger of explosion, so the PUW explosion-proof valve becomes a breakthrough and can quickly relieve pressure time.
- Waterproof and shock resistance in the pack structure of the lithium battery bag is very important. Speaking of which, the battery pack is actually complex. It involves many aspects, but it would be good if the details could be done well.
- Integration of lithium battery pack structure design: After the end of a single module pack, they should be connected in series to form a battery cell. At this time, the series connection between each other should be considered to meet the form of a fast and safe series interface.
- Internal insulation design of battery pack structure: The insulation of the positive and negative poles have been taken into account when designing the structure, but the uncertainty of the on-board battery is too complicated, so the insulation conditions must be set separately in the process of pack battery design to meet the requirements of impact, vibration, humidity, etc. The battery is still safe and effective in complex environments.
Conclusion
In the combination of pack lithium battery packs, in addition to the safety and reliability of the battery packs, the control of the protection level, refrigeration, and heating, especially in terms of the method of battery connection, and consider the accuracy of BMS measurement. This problem is common, ignoring the impact of pressure drops on testing, resulting in the battery pack’s balanced ability.
More Articles:
BMS Function Analysis of Battery Management System,
Battery Vulcanization,
The Charge Status of Lithium Batteries.,
How to distinguish between good and bad electric vehicle tires,
How many other signs on the battery do you know?
How to run smooth Electric Vehicles even in rain,
Flexible-Failure and Rigid Failure,
Principles of Power Battery Cooling System,
How Many Degrees Of Electricity Does An Electric Car Need To Be Filled At A Time,
Battery Repair System Product Description And Overview,
Analysis of Common Terms for Lithium Batteries,