Introduction
The power battery system is usually composed of battery cells, battery management system, Pack system including functional components, wiring harness, structural parts and other related components. The failure mode of the power battery system can be divided into three different levels of failure modes, namely the cell failure mode, the Cell BMS Pack Failure Analysis
Cell Failure Mode
The failure modes of cells can be further divided into safety failure modes and non-safety failure modes.
The Safety Failures of Battery Cells Mainly include the Following Points:
1. The Positive and Negative Electrodes Inside the Cell are Short-Circuited:
The short circuit in the battery is caused by the inside of the cell. There are many reasons for the short circuit in the battery, which may be caused by defects in the production process of the battery cell or due to the deformation of the battery cell caused by long-term vibration and external force. Once a serious internal short circuit occurs, the control cannot be prevented, the external insurance does not work, and smoking or burning will definitely occur.

2. Battery Cell Leakage:
This is very dangerous and a very common failure mode. Many electric vehicle fire accidents are caused by battery leakage. The reasons for battery leakage include: external force damage; damage to the sealing structure caused by collision and irregular installation; manufacturing reasons: welding defects, insufficient sealing glue and poor sealing performance.
After the battery leaks, the insulation of the entire battery pack fails, and the single point insulation failure is not a big problem. If there are two or more insulation failures, an external short circuit will occur. From the perspective of practical application, soft pack and plastic case cells are more prone to leakage and insulation failure than metal shell cells.
3. Lithium Precipitation in the Negative Electrode of the Battery:
Improper use of the battery, overcharging, low-temperature charging, and high-current charging will lead to lithium precipitation in the negative electrode of the battery. Lithium iron phosphate or ternary batteries produced by most domestic manufacturers will undergo lithium precipitation when charged below 0 degrees Celsius, and can only be charged with small currents above 0 degrees Celsius according to the characteristics of the cells. After the negative electrode lithium precipitation occurs, the lithium metal cannot be reduced, which leads to the irreversible decay of the battery capacity. Lithium precipitation reaches a certain degree of severity, lithium dendrites are formed, and an internal short circuit occurs when the separator is pierced. Therefore, the power battery should be strictly forbidden to be charged at low temperature when in use.
4. The Battery is Inflated:
There are many reasons for flatulence, mainly because the side reaction inside the battery produces gas, the most typical one is the side reaction with water. The flatulence problem can be avoided by strictly controlling the moisture in the cell production process. Once the battery is flattened, there will be leakage and so on.
The above failure modes are very serious problems and may cause casualties. Even if a battery cell is used for 1 or 2 years without problems, it does not mean that there will be no problems with the battery cell in the future. The longer the battery is used, the greater the risk of failure.
Buy Now: SEMCO provide high-quality Battery Balancer to measure the voltage, resistance, and more.
The Non-Safety Failure of the Cell only Affects the Performance, Mainly in the Following Points:
1. Poor Capacity Consistency:
The inconsistency of power batteries usually means that the residual capacity of the batteries in a group of batteries is too different and the voltage difference is too large, causing the battery life to deteriorate. There are many reasons for the poor consistency between batteries, including the manufacturing process of the battery, the storage time of the battery, the temperature difference during the charging and discharging of the battery pack, and the magnitude of the charging and discharging current.
2. Excessive Self-Discharge:
The irreversible reaction caused by the micro-short circuit caused by impurities during battery manufacturing is the main reason for the excessive self-discharge of individual batteries. In most battery manufacturers, the micro-hour self-discharge of the battery can be ignored. Due to the chemical reaction of the battery with the environmental conditions during the long-term charge-discharge and shelving process, the battery has a large self-discharge phenomenon, which reduces the battery capacity and reduces its performance. Low, cannot meet the needs of use.
3. Reduced Discharge Capacity at Low Temperature:
As the temperature decreases, the low temperature performance of the electrolyte is not good, the participation in the reaction is not enough, and the conductivity of the electrolyte decreases, resulting in an increase in the battery resistance, a decrease in the voltage platform, and a decrease in the capacity. At present, the discharge capacity of batteries of various manufacturers at -20 degrees is basically 70% to 75% of the rated capacity. At low temperature, the discharge capacity of the battery decreases, and the discharge performance is poor, which affects the performance and driving range of the electric vehicle.
4. Battery Capacity Decay:
The battery capacity attenuation mainly comes from the loss of active lithium ions and the loss of electrode active materials. The regularity of the layered structure of the positive electrode active material decreases, the passive film is deposited on the negative electrode active material, the degree of graphitization decreases, and the porosity of the separator decreases, resulting in an increase in the charge transfer resistance of the battery. The ability to deintercalated lithium decreases, resulting in a loss of capacity.
Buy Now: SEMCO provide high-quality IR (Internal Resistance) Tester Machine.
BMS Failure Mode
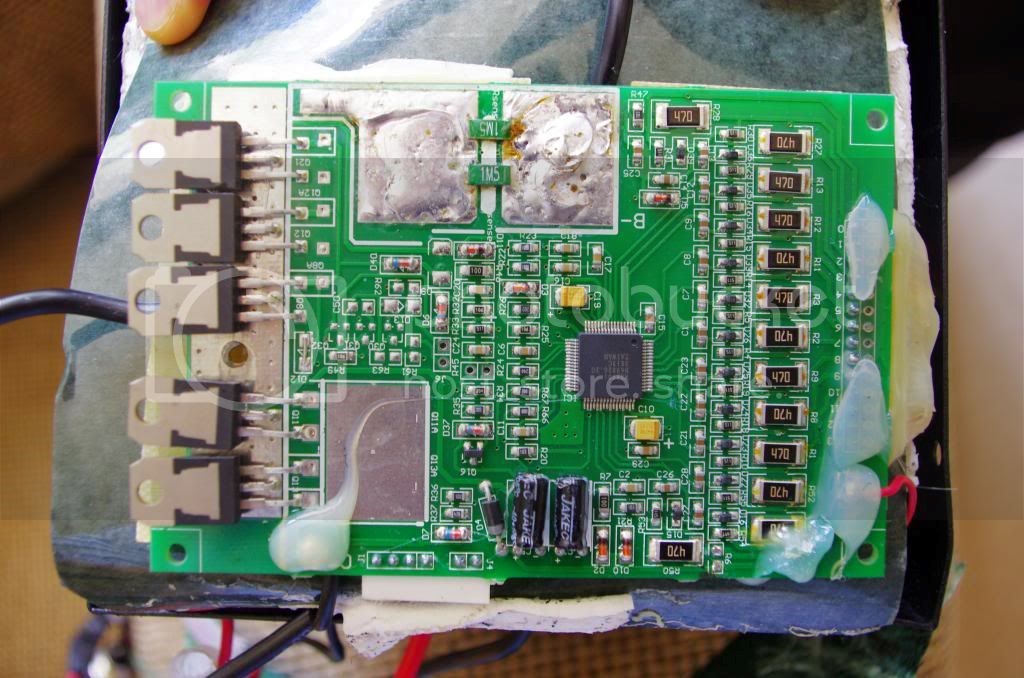
The single failure of the battery is not only related he battery itself, but also to the failure of the battery management system BMS. BMS failure modes can also cause serious accidents in the following categories:
1. The Failure of BMS Voltage Detection Causes the Battery to be Over-Charged or Over-Discharged:
The connection, crimping process or poor contact lead to the failure of the voltage detection line, the BMS has no voltage information, and the charging does not stop when it should be stopped. If the battery is overcharged, it will catch fire and explode. If the lithium iron phosphate is overcharged to more than 5V, most of it will only emit smoke, but once the ternary battery is overcharged, it will explode.
2. BMS Current Detection Failure:
The Hall sensor fails, the BMS cannot collect current, the SOC cannot be calculated, and the deviation is large. Failure of current detection may result in excessive charging current. The charging current is large, the heat inside the cell is large, and the temperature exceeds a certain temperature, which will weaken the curing capacity of the diaphragm and seriously affect the battery life.
3. BMS Temperature Detection Failure:
The failure of temperature detection leads to the high working temperature of the battery, and the irreversible reaction of the battery occurs, which has a great impact on the battery capacity and internal resistance. The battery’s calendar life is directly related to the temperature. The number of cycles at 45 degrees is half of that at 25 degrees. In addition, if the temperature is too high, the battery is prone to problems such as bulging, leakage, and explosion. Therefore, the temperature of the battery should be strictly controlled during the use of the battery.
4. Insulation Monitoring Failure:
Insulation failure will occur when the power battery system is deformed or leaked. If the BMS is not detected, electric shock may occur. Therefore, the BMS system should have the highest requirements for monitoring sensors, and avoiding the failure of the monitoring system can greatly improve the safety of the power battery.
5. Communication Failure due to Electromagnetic Compatibility Issues:
For BMS system, electromagnetic compatibility mainly evaluates its anti-electromagnetic interference ability. Electromagnetic interference will cause the failure of BMS communication and cause the above problems.
6. Large Deviation in SOC Estimation:
At present, the common problem of all BMS manufacturers is the difference in deviation size. Basically, the current inspection standard requirements are within 5%, and it should be difficult for most manufacturers to achieve BMS, because the SOC error will become larger and larger in actual use, because the use environment is more complex, and there are more conditions affecting the accuracy.
Three, Pack System Integration Failure Mode
1. Failure of the Busbar:
If it is a bolted connection, in the later use process, the oxidation of the bolt or the loosening of the bolt will cause a lot of heat to be generated at the conductor connection, and in extreme cases, the power battery will catch fire. Therefore, most power battery system manufacturers use laser welding at the connection between the cell and the cell or the connection between the module and the module during the pack design, or add a temperature sensor at the connection to avoid the failure of the bus bar by means of detection.
2. The Main Circuit Connector of the Power Battery System Fails:
The high-voltage line of the power battery system is connected to the external highvoltage system through the connector. The performance of the connector is unreliable, and virtual connection occurs under vibration, resulting in high temperature ablation of the connector. Generally speaking, the connection failure will occur when the connector temperature exceeds 90 degrees. Therefore, when designing the system, the connector needs to add a high-voltage interlock function, or attach a temperature sensor to the connector to monitor the temperature of the connector at all times to prevent the failure of the connector.
3. The High-Voltage Contactor is Sticky:
The contactor has a certain number of load openings, and most of the contactors are ablated when the high current is closed under load. In the system design, the double relay scheme is generally used, and the control is closed in sequence to avoid sticking of the high-voltage contactor.
4. The Fuse Over-Current Protection Fails:
The selection and matching of the fuses in the high-voltage system components, and which one to break first and which one to break later in the gradient needs to be comprehensively considered. Vibration or external collision and extrusion lead to deformation of the power battery, seal failure, and IP rating reduction. Therefore, it is necessary to consider the collision protection of the battery box structure when designing the system.
Buy Now: SEMCO Lithium Ion Battery Sorting Machine Manufacturer
Conclusion
According to the various failure modes of the above power battery systems, researchers and battery manufacturers need to improve the safety of lithium battery cells by continuously improving processes and technologies. BMS system manufacturers should fully understand the performance of batteries, based on the safety design principles of power batteries, designing a safe and reliable battery system and correct use is the ultimate barrier to ensure battery safety. Users should use the power battery system correctly, prevent mechanical abuse, thermal abuse and electrical abuse, and effectively improve the safety and reliability of electric vehicles.
More Articles:
Key Points of Lithium-Ion Battery Production Process Control,
How to Choose a High Quality Electric Vehicle Charger,
Lithium-ion Battery Packaging Information for Beginners,
Lithium Battery Protection Board,
Basic Knowledge of Lithium-ion Battery Commercialization,
Action protector in electric vehicle charging system,
History of Lithium Battery Development,
Production problems of lithium batteries,
Formation Process of Lithium Battery,
How the Three Electrode System Works,
Electric Vehicle Maintenance Practical Dry Goods,