Introduction
As electric vehicle maintenance (and electrification technologies) become more popular with consumers and ecosystem players, there is a growing focus on ethical and sustainability issues in operations and processes across the value chain. From mining practices to battery cascade utilization, ecosystem players hope to double down on sustainability by implementing more ethical standards throughout the battery life cycle.
There will be some big and small problems when we ride electric vehicles for a long time. How can we get through the key point quickly and accurately when repairing electric vehicles? There are many parts for electric vehicles, and maintenance is essentially the repair and replacement of parts. So, This Article explains possible failures from key parts to help you repair them quickly.
1. Frame
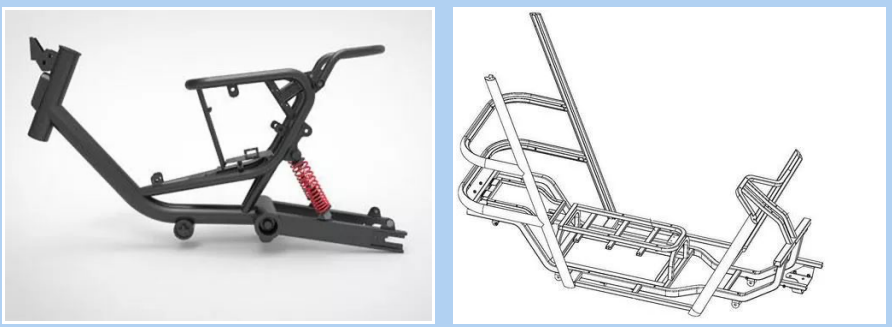
The frame can be said to be the safety core of a car:
- If it is found that the whole car always tilts one side when riding, it may be that the whole vehicle is tilted.
- If the whole car has a serious concave, it may be overloaded and ride in poor road conditions, resulting in the deformation of the whole vehicle. The possibility of deformation is that there is a crack in the front riser pipe and the front triangle welding, or crack in the joint of the saddle pipe flat fork and the frame.
- If there is a rattling metal knocking sound, there may be a problem with the strength or welding of some joints.
Buy Now: SEMCO Infratech – Fully Automatic Lithium Battery Equalizer A 24 Way
2. Back Flat Work
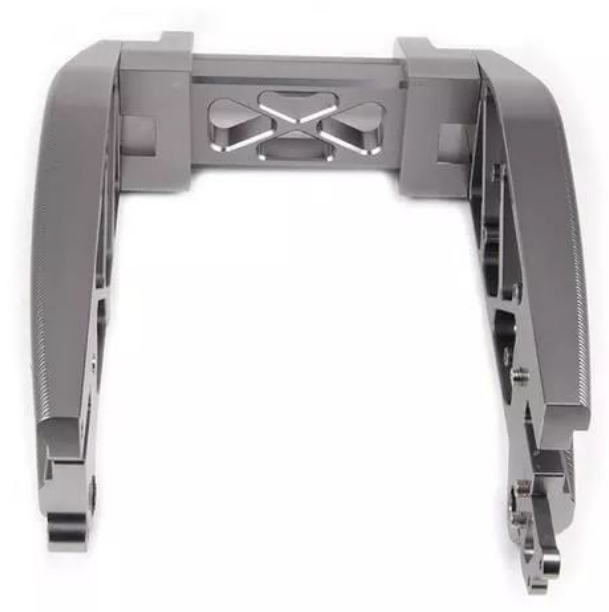
When the rear wheel swings when we ride, the rear swings when braking, the vehicle shakes when riding at high speed, and the chain drops when the pedal is strong, the rear fork screws are loose. When the above problems occur, you need to tighten the nut and return half a circle, so that it is not easy to loosen.
3. Fork
The fork is more likely to be damaged. General collisions and powerful dive will damage the fork springs. The damage will directly cause the front wheel mud plate to touch the front triangle or the front wheel will collide with the plastic parts, and the electric vehicle will not be able to turn. So how to solve this problem? It’s very simple. Just press the front fork with greater force to see the gap to decide whether to change the front fork or increase the gap.
4. Handles and Riser
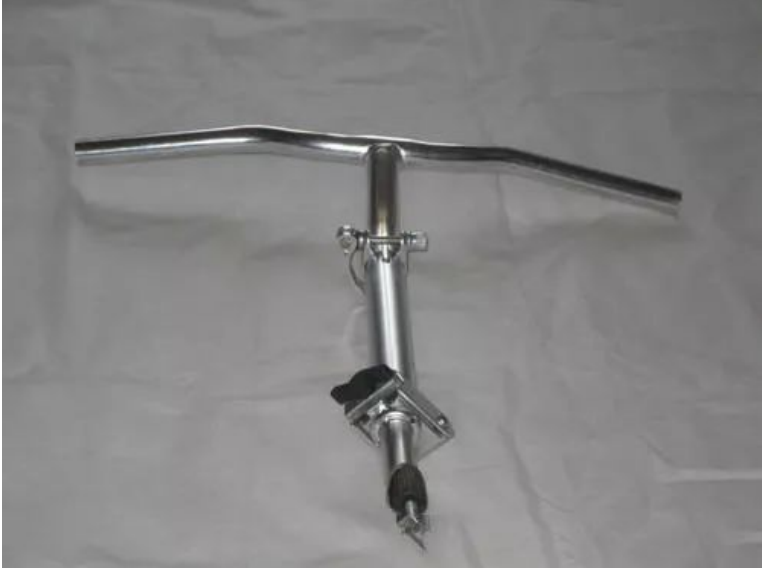
Long-term use will rust the handle and riser. At this time, the screws should not be strongly screwed. It should be treated with rust agent for a period of time, and then carefully knocked on the outside of the front riser with an iron hammer. When twisting the screws, it is best to use a plum wrench or a socket wrench. Generally, there is no rigid hand or a live contact wrench.
Buy Now: Semco 12V Vehicles Battery Tester for any Type of Vehicle Battery
5. Cable
Cable damage is generally rare, but once touched, it becomes difficult to solve because the cause is difficult to find. Then during repair, you can first find the area where the problem may occur according to the function of the controller or display, and then find the connection of the cable according to the corresponding colour to find the problem cable.
6. Controller

Damage to controllers is generally common, manifested in the fact that the motor does not rotate, the rotation noise is loud, the time does not rotate, the time is forward and the time is reversed, the controller temperature rises, the motor is weak, etc.
- For controllers, the failure of the motor may be interference from the brake electrical signal or the reset of the single-chip microcomputer, and the high rotation noise may be a problem with the continuation of the CMOS tube or the phase error.
- Non-rotation may be the poor contact of the controller-powered power supply, and the reverse may be virtual welding of the pin controlling the forward and reverse in the controller.
- The rapid temperature rise of the controller may be an increase in the current consumed by the controller itself. Generally, the consumption current is 30-40mA, or there is a problem with the operation of the CMOS tube. The weakness of the motor may be caused by the poor welding of the overcurrent copper wire, resulting in the inability to pass through high current.
7. Motor
We mainly judge the performance of the motor with the following indicators:
Motor noise. Noise is available in each motor, but there can be no noise of metal collision, marble extrusion and friction, allowing uniform electromagnetic noise, which can be monitored on the motor shaft through hollow metal listening rods.
● Motor is on-board current. The detection of the no-load current of the motor mainly reflects the demagnetization of the motor and the wear loss of the machinery. If the current increases and the no-load speed of the motor increases, it generally shows that the demagnetization phenomenon is obvious.
● Motor load current. Detecting the load current of the motor mainly reflects the actual operating efficiency of the motor. If the load current increases, but the actual torque is small, it means that the efficiency of the motor is very low. It is necessary to check the magnetic energy volume of the magnetic steel. In addition, the welding inside the coil should also be paid attention to. If there is a brush motor, it is necessary to check whether the commutator has a short circuit. Phenomenon. Brushless motor Hall is commonly used in switching. When on-line detection, it mainly tests whether the Hall signal changes correctly. Generally, high and low voltage rotations, and the number of changes are half of the number of magnetic steels
If you carefully check the voltage changes of each line, you can find that it is a regular 6 repeat cycles. For 120 degrees, the motor change should be 100, 110, 010, 011, 001 and 101, and for 60 degrees, the motor change should be 100, 110, 111, 011, 001. 000. In addition, when repairing Hall without brush motors, you should pay attention to Hall’s model. When welding, you must wear anti-static gloves or wrist guards. Electric soldering irons are best soldered offline, and pay attention to Hall’s front and back. When repairing the carbon brush of the brush motor, first put the carbon brush into the brush grip, tighten the soft copper lead of the carbon brush and fix it in the lead groove. After the internal stator is fully put into the outer rotor, relax the carbon brush and check the flexibility of the carbon brush.
8. Battery
Lead-acid batteries and lithium batteries are generally used now.
The formal testing of lead-acid batteries must test the actual capacity. Generally, 0.5C is the standard discharge, and C is the capacity value of 2h rate. If the capacity value specified by the manufacturer is not reached, it can be replaced during the repair period. When servicing lead-acid batteries, they can be easily detected in the following ways:
- Measure the end voltage of the battery and test the short-circuit current of the battery. If the end voltage of the battery is high, but the spark is very small in the short circuit, it means that the battery has open circuits. Generally, there are fewer cases of welding fractures in the internal plate. Pay attention to checking the virtual welding of the exposed terminal and the serious corrosion of the electrode.
- Measure the voltage at the battery end immediately after being fully charged, then place it for more than 5 hours, and detect the end voltage again. If the voltage drops greatly, and it still drops at a large amplitude during the measurement process, it means that the battery self-discharge is very serious and generally needs to be replaced.
- During the charging process, the battery is seriously hot, but the battery has not been deformed, you need to check the charging current of the charger. Generally, the charging current of the 10-14Ah battery is about 1.6-1.8A, and the charging current above 17Ah-20Ah is about 2.5-3.0A. The battery will lose moisture due to severe heat, so it needs to be rehydrated.

9. Light Bulb
We can’t underestimate the accessories of electric vehicle light bulbs. The public use of existing double-filament bulbs is very different. If they are not matched well with the cable, the light bulb will work abnormally, which will seriously lead to the fact that the headlights will not move as soon as the headlights are turned on. We should be paid attention to this part.
More Articles:
Lithium-ion Battery Packaging Information for Beginners,
Lithium Battery Protection Board,
Basic Knowledge of Lithium-ion Battery Commercialization,
Action protector in electric vehicle charging system,
History of Lithium Battery Development,
Production problems of lithium batteries,
Formation Process of Lithium Battery,
Model S Plaid Battery System Design,
Battery Pole Piece Coating Process,
Point Defects in Pole Piece Coating,