Introduction
The production process of lithium battery cell consists of three main processes steps: electrode manufacturing, cell assembly and cell finishing.
- Electrode production and cell finishing are largely independent of the cell type, while within cell assembly a distinction must be made between pouch cells, cylindrical cells and prismatic cells.
- Regardless of the cell type, the smallest unit of any lithium-ion cell consists of two electrodes and a separator, which separates the electrodes from each other. The ion-conductive electrolyte fills the pores of the electrodes and the remaining space inside the cell.
Lithium-ion battery is a complex system, including positive electrode, negative electrode, separator, electrolyte, current collector and binder, conductive agent, etc.
Lithium batteries can be divided into cylindrical batteries, square batteries and soft pack batteries according to their shape, and their production processes are different to some extent, but the overall lithium battery manufacturing process can be divided into the front process (pole piece manufacturing), the middle process (cell synthesis), The back-end process (chemical packaging). Due to the high safety performance requirements of lithium-ion batteries, there are extremely high requirements for the precision, stability and automation level of lithium-ion batteries in the battery manufacturing process.
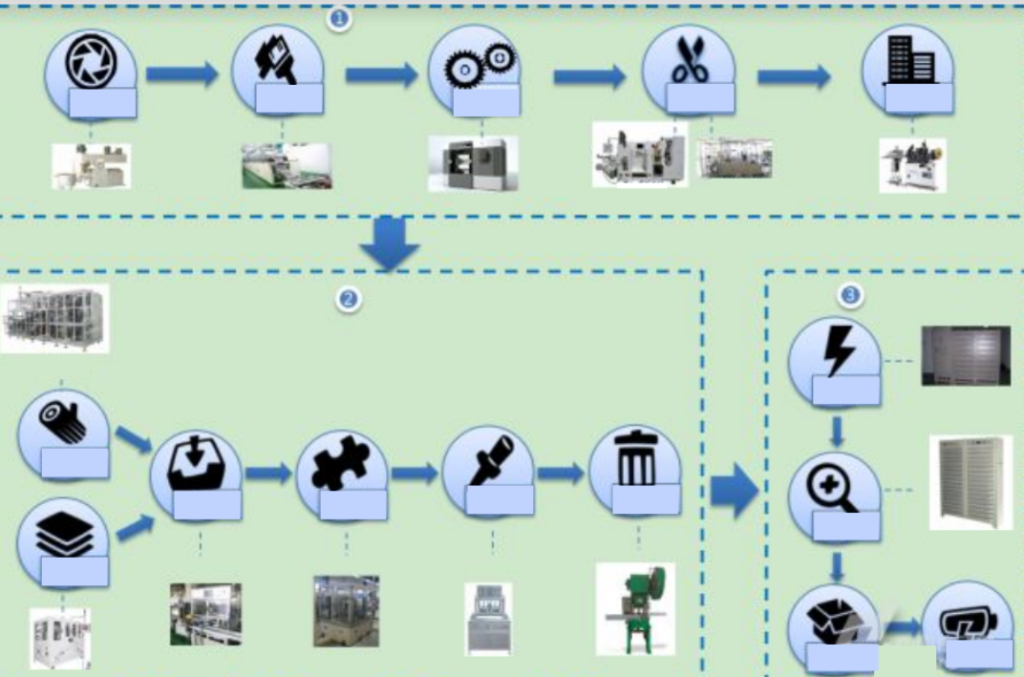
Lithium battery equipment is a process equipment that manufactures and produces positive and negative electrode materials, diaphragm materials, electrolytes and other raw materials through an orderly process. Lithium battery equipment has a significant impact on the performance and cost of lithium batteries., is one of the determining factors. According to different technological processes, lithium battery equipment can be divided into front-end equipment, middle-end equipment, and back-end equipment
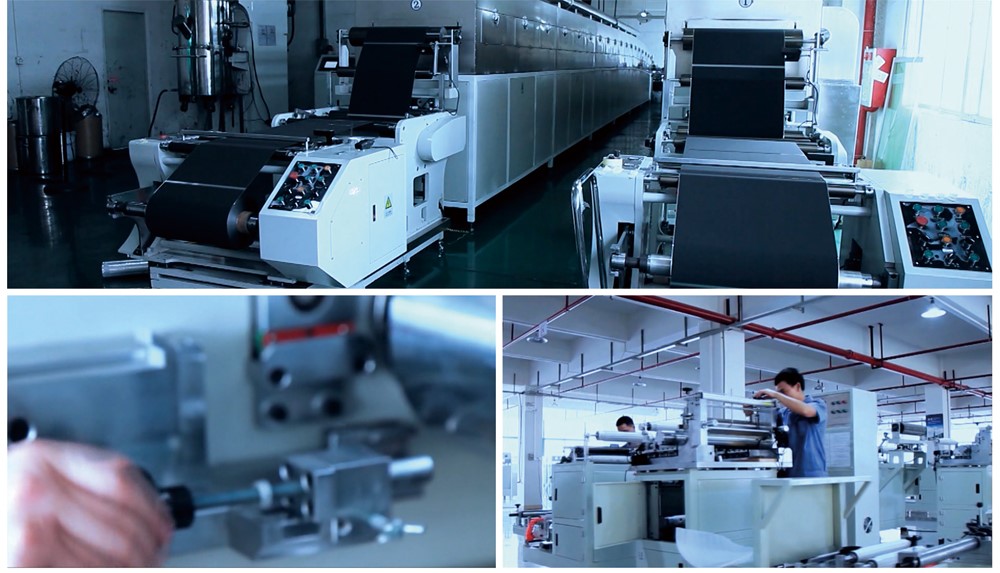
Buy Now: SEMCO Battery Charge & Discharge Cabinet Tester SI BCDS 99V – 20A – 1CH.
The production goal of the previous process is to complete the manufacture of (positive and negative) pole pieces. The main processes of the front-end process are: stirring, coating, rolling, slitting, filming, and die-cutting. The equipment involved mainly includes: mixer, coating machine, rolling machine, slitting machine, tableting machine, die-cutting machine etc.
- Slurry stirring (equipment used: vacuum mixer) – is to mix the positive and negative solid-state battery materials evenly, then add solvent and stir into a slurry. Slurry stirring is the starting point of the previous process, and it is the pre-process basis for the completion of subsequent coating, rolling and other processes.

Coating (equipment used: coating machine) – is to uniformly coat the stirred slurry on the metal foil and dry it to make positive and negative electrodes. As the core link of the previous process, the execution quality of the coating process has a profound impact on the consistency, safety and life cycle of the finished battery, so the coating machine is the most valuable equipment in the previous process.
Rolling (equipment used: rolling machine) – is to further compact the coated pole pieces, thereby increasing the energy density of the battery. The flatness of the pole piece after rolling will directly affect the processing effect of the subsequent slitting process, and the uniformity of the active material of the pole piece will also indirectly affect the performance of the cell.

Slitting (equipment used: slitting machine) – is to continuously slit a wide whole roll of pole pieces into several narrow pieces of required width. The pole piece encounters shearing failure during slitting, and the smoothness of the edge after slitting (no burr, no buckling) is the key to examining the performance of the slitting machine.

Filming (equipment used: filming machine) – includes welding the tabs, sticking protective tape, wrapping the tabs, or using laser cutting to form the tabs, etc., for the subsequent winding process. Die-cutting (equipment used: die-cutting machine) is to die-cut the coated polepiece for subsequent processes.
The production goal of the mid-stage process is to complete the manufacture of cells. There are differences in the technical route and production line equipment of the mid-stage process of different types of lithium batteries.
Winding (equipment used: winding machine) – It is a battery cell that winds the pole pieces made by the film making process or winding die-cutting machine into lithium-ion batteries, and is mainly used for the production of square and round lithium batteries. Winding machine can be subdivided into two categories: square winding machine and cylindrical winding machine, which are used for the production of square and cylindrical lithium batteries respectively. Compared with cylindrical winding, the square winding process has higher requirements for tension control, so the square winding machine is more difficult technically.
Lamination (equipment used: laminator) – It is a cell that stacks a single polar piece made in the die-cutting process into a lithium-ion battery, and is mainly used for the production of soft pack batteries. Compared with square and cylindrical cells, soft-packed batteries have obvious advantages in terms of energy density, safety, and discharge performance. However, the lamination machine completes a single stacking task, involving multiple sub-processes in parallel and complex mechanism coordination, and improving the lamination efficiency needs to deal with complex dynamic control problems; while the winding machine speed and winding efficiency are directly related, and the means of efficiency improvement are relatively simple. At present, there is a gap between the production efficiency and yield of laminated batteries and the winding batteries.
Liquid injection machine (equipment used: liquid injection machine) – It is to quantitatively inject the electrolyte of the battery into the battery cell.
Battery cell packaging (equipment used: shelling machine, groove roller, sealing machine, welding machine) – It is to put the core into the battery cell housing.
The production goal of the segment process is to complete the packaging. As of the middle stage of the process, the functional structure of the lithium battery cell has been formed, and the significance of the later stage of the process is to activate it, after testing, sorting and assembly, to form a safe and stable lithium battery finished product. The main processes of the later stage of the process are: formation, capacity, testing, sorting, etc., the equipment involved mainly includes: charging and discharging motors, testing equipment, etc.
Chemical Formation (equipment used: charge and discharge motor). The battery cell is activated through the first charge, during which an effective passivation film (SEI film) is generated on the negative surface to achieve the “initialization” of the lithium battery. Capacity (equipment used: charge and discharge motor). That is, “analysis capacity”, is to charge and discharge the formed battery according to the design standard to measure the capacitance of the battery cell. The battery cell is charged and discharged through the process of formation and capacity separation, so the charge and discharge motor are the most commonly used rear core equipment. The smallest unit of operation of a charge-discharge motor is a “channel”, and a “unit” (BOX) consists of several “channels” Combined, multiple “units” are combined to form a charge and discharge motor.
Testing (Equipment used: Testing equipment) – Before and after charging, discharging, and standing; Sorting According to the test results, the batteries after chemical formation and capacity are classified and selected according to certain standards. The significance of the inspection and sorting process is not only in order to eliminate unqualified products, because in the practical application of lithium-ion batteries, the cells are often combined in parallel and series, so the selection of cells with similar performance helps to achieve the best overall performance of the battery.
Conclusion
To Conclude the production process of lithium battery includes: batching, coating, filming (cutting, roll pressing), auxiliary material processing, core processing, spot welding and edge sealing, liquid injection, forming, air extraction, and volumetric inspection. The production of lithium batteries is inseparable from lithium battery production equipment, in addition to the materials used in the battery itself, manufacturing craftsmanship and production equipment is an important factor in determining the performance of the battery.
More Articles:
Introduction to Cell Balancing System,
Intercontinental Battery Circle,
Application of Isolation testing Technology,
Battery separator material,
History of Lithium Battery Development,
Production problems of lithium batteries,
Formation Process of Lithium Battery,
Principles of Power Battery System Design,
Battery Pole Piece Coating Process,
Point Defects in Pole Piece Coating,