Basic principles of power battery system design
The selection of electric vehicle batteries is closely related to parameters such as capacity, internal resistance, battery type, and production specifications. When selecting a single battery, the performance parameters, safety, energy density of the single battery and the installation position, space, total energy and power of the battery pack should be considered. The following uses a case to describe the battery selection in detail.
Battery Pack Design Input:
- Cruising range: 100 km
- Energy consumption factor: 0.15 kWh/km
- Drive voltage: DC 350 V (DC side voltage of drive motor and controller)
- Continuous current: 1C output
- P/E value: 5
- Battery type: soft pack ternary lithium battery
- Battery Specification: 20Ah / 3.6V
Buy Now: SEMCO Battery Charge & Discharge Cabinet Tester SI BCDS 100V 10/20A 7CH.
Battery Pack Design Output:
Project | Parameter | Formula |
Total capacity of battery pack system | ≥ 15kWh | = design mileage * energy consumption coefficient |
Total battery pack system usable capacity | ≥ 12kWh | = total capacity * SOC operating range |
Battery pack system SOC operating range | ≥ 80% | = 10% SOC~90%SOC |
Battery system nominal voltage | DC 350V | = drive voltage |
Battery system operating voltage range | DC 287V~408V | = 3V~4.2V |
Battery system continuous charge/discharge power | 15 kW | = 1C continuous output capability |
Battery system peak charge/discharge power | 60kW @ 10s | = P/E |
Battery system operating temperature range | 0℃~60℃ | – |
Battery system cooling method | – | – |
Battery system life | 8 years | = 8 years or 100,000 km |
Battery system self-discharge rate | May | – |
Total weight of battery system | ≤ 150kg |
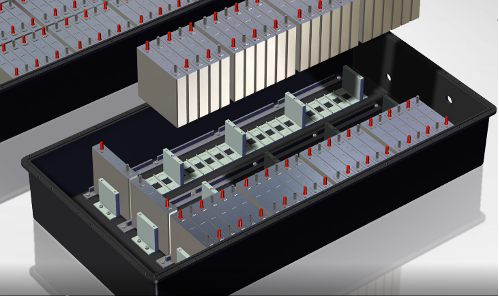
Module Design Output:
- Number of module strings = driving voltage/battery rated voltage = 350V/3.6V ≈ 98 strings
- Number of modules in parallel = total energy/number of strings/cell voltage/single capacity =15kWh/98 strings/3.6V/20Ah ≈ 2 parallels
- Serial and parallel mode =
- first parallel then serial
- Serial-before-parallel
Buy Now: SEMCO Battery Charge & Discharge Cabinet Tester SI BCDS 99V – 20A – 1CH.
Parallel First and then Serial:

In the parallel-before-series structure, the failure of a single battery automatically exits, except for the capacity reduction, it does not affect the use after parallel connection, and the parallel connection process is strict; when a unit battery in the parallel connection is short-circuited, the parallel circuit current is very large, which is usually avoided by adding fuse protection technology. Therefore, the scheme chooses the parallel process first and then the series process.
Project | Parameter | Remark |
The number of modules in series and parallel | 98 series 2 parallel | |
Serial mode | Serial first | |
Module voltage range | 294V~411.6V | |
Module rated voltage | 352.8V | |
Module pressure | 800N ~ 1000N |
Battery Design Output:
Project | Parameter | Remark |
Battery Type | Soft pack ternary lithium battery | |
Single battery voltage range | 3.0V ~ 4.2V | |
Single battery capacity | 20Ah | @1C |
Single battery nominal voltage | 3.6V | |
Cycle life | ≥ 3000 times | @1C |
In the battery module design process, the safety specification test parameter level of the battery module should be higher than the safety specification level of the battery pack to improve the reliability of the battery pack. The specific module requirements are as follows:
Module open circuit voltage | The OCV between the total positive and total negative of the measuring module for the mustimeter |
Module cell voltage | Test tooling to measure the OCV voltage of each string of batteries, ΔV≤5mV~10mV |
Module DC internal resistance | The device charges or discharges the module with a 3C rate of10s, and measures the DCIR |
Module AC internal resistance | ACR test the module at 1kHz |
Module insulation resistance | The total positive and total negative of the module to the insulation internal resistance between metals |
Module withstand voltage | The total positive and total negative of the module to the electrical clearance of the housing |
The above is the preliminary design of the battery system. Note that the BMS design is not included in this design.
Battery Process:
- Boutique | Cathode ingredients for lithium batteries
- Boutique | Negative electrode ingredients and coating for lithium batteries
- Boutique | Roller and slitting of lithium battery
- Boutique | Cathode Coating
- Boutique | Lithium battery into the shell and rolling groove
- Boutique | Lithium battery cell baking, liquid injection and super welding cap
- Boutique | Sealing and cleaning of lithium batteries
- Boutique | Formation and capacity distribution of lithium batteries
Battery Design:
- Design of Soft Wrapped Winding Battery – Electrochemical Design
- Design of Soft Wrapped Winding Battery – Structural Design
- [Dry goods] Lithium button battery assembly and test
Design Theory:
- Theoretical Calculation of Lithium Battery Slurry Sedimentation
- Lithium battery pole piece design theory
- [Dry goods] Theoretical formula for the design of lithium battery tabs
- The working principle of the battery cap [Part 1]
- The working principle of the battery cap [Part 2]
- Influence of physical and chemical parameters of lithium iron phosphate battery raw materials on electrical properties (1)
- Influence of physical and chemical parameters of lithium iron phosphate battery raw materials on electrical properties (2)
Battery Material Testing and Evaluation Standards:
- Test methods and standards for cathode materials (continued)
- Test methods and standards for negative electrode materials
- Test methods and standards for diaphragm materials
- [Dry goods] Test method for HF (hydrofluoric acid) in electrolyte
- Test methods and standards for NMP
- Test methods and standards for electrolyte materials
- Test methods and standards for KS-6
- Test methods and standards for water-based adhesives
- Test methods and standards for Super-P
- Test methods and standards for aluminium foil
- Test methods and standards for copper foil
- [Dry goods] Electrolyte moisture test method
- Test methods and standards for CMC
- [Popularity] Contents of battery electrical performance test
- [Popularity] Battery safety performance test project
Conclusion
When designing a battery bank for a specific location, a good design will ensure that the battery bank is perfectly: sized so the energy capacity matches the load requirements. sized for maximum and minimum voltage requirements for the desired application.
More Articles:
Introduction to Cell Balancing System,
Lithium ion battery fire accidents occur frequently, what is the reason?,
Analysis and summary of lithium battery,
IEC Battery Safety Standard for Power Batteries,
POWER BATTERY SHELL WATERPROOF DESIGN,
Production problems of lithium batteries,
Aging Mechanisms of Li-ion Batteries.