The manufacturing landscape has witnessed remarkable advancements over the years, especially in the realm of battery production. Among the critical technologies that have revolutionized battery manufacturing, laser welding machines stand out for their precision, efficiency, and ability to meet the demands of modern energy storage systems. This article delves into the fascinating journey of battery laser welding machines, tracing their roots from the conceptual stage to their current state-of-the-art form.
I. The Emergence of Laser Welding
The foundation of laser welding technology dates back to the early 1960s when Theodore Maiman developed the first working laser. Initially, it found applications in research, military, and medical fields. As the technology matured, researchers began exploring its potential in industrial applications, including welding.
II. Early Experiments in Laser Welding
In the 1970s, researchers started conducting experiments with laser welding techniques. However, early laser welding machines were limited by their power and size, making them unsuitable for battery production, which required intricate and precise welding.
III. The Advent of Battery Laser Welding Machines
By the 1980s, advancements in laser technology allowed for the development of more powerful and compact laser sources. This led to the birth of battery laser welding machines. These machines were designed to address the specific welding challenges posed by battery components, such as thin and delicate materials, ensuring minimal heat-affected zones and reduced thermal stress.
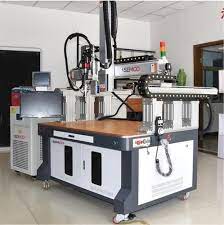
IV. Refining Precision and Accuracy
As the demand for high-performance batteries increased, so did the need for enhanced welding precision and accuracy. Researchers and manufacturers collaborated to optimize laser welding parameters and improve control systems. This refinement resulted in reduced defects, improved joint quality, and increased productivity.
V. Integration of Robotics and Automation
In the late 1990s and early 2000s, the integration of robotics and automation into battery laser welding machines transformed the manufacturing landscape. Robotic systems enabled the seamless handling of battery components during welding, enhancing repeatability and minimizing human error.
VI. Advancements in Beam Delivery Systems
The development of sophisticated beam delivery systems further bolstered the capabilities of battery laser welding machines. Fiber optics and galvanometer-based systems enabled precise and flexible beam positioning, facilitating welds in complex battery designs with tight spatial constraints.
VII. Addressing Material Compatibility
Battery production involves diverse materials, and welding dissimilar materials presented a challenge for laser welding machines. In response, researchers developed innovative techniques like hybrid laser welding and pulse shaping to address material compatibility issues, ensuring robust and reliable welds in multi-material battery designs.
VIII. In-line Quality Control and Monitoring
To meet the stringent quality standards of the battery industry, laser welding machines incorporated in-line quality control and monitoring systems. Real-time monitoring of weld quality allowed for early detection of defects and deviations, enhancing the overall production efficiency and minimizing scrap rates.
IX. Laser Welding in Electric Vehicle Battery Production

With the rise of electric vehicles (EVs), battery laser welding machines found a prominent role in the manufacturing of EV batteries. Their ability to join thin foils and maintain uniform welding quality played a crucial role in the mass production of battery packs, contributing to the global EV revolution.
X. Advancements in Pulse Power and Ultrafast Laser Welding
Recent advancements in pulse power and ultrafast laser technology opened up new possibilities for battery welding. These technologies offer precise control over heat input and minimized heat-affected zones, making them ideal for welding delicate battery components with unprecedented precision.
Conclusion
The journey of battery laser welding machines from concept to reality has been marked by continuous innovation and collaboration between researchers, manufacturers, and the broader energy storage industry. Today, these machines play a pivotal role in ensuring the reliability, efficiency, and safety of modern battery systems. As technology continues to evolve, battery laser welding machines are poised to shape the future of energy storage and drive further advancements in electric mobility and renewable energy integration.