Hydrogen fuel cells have gained significant attention as a clean and efficient alternative to traditional combustion engines. These fuel cells generate electricity through a chemical reaction between hydrogen and oxygen, with water as the only byproduct. To harness the potential of hydrogen fuel cells, a complex production process is involved. This article delves into the detailed steps of the hydrogen fuel cell production process, from the sourcing of raw materials to the creation of a clean energy source.
Raw Material Sourcing:
The production process begins with the sourcing of raw materials required for hydrogen fuel cell manufacturing. The key materials include platinum or other catalysts for electrode reactions, polymers for the electrolyte membrane, and carbon-based materials for the bipolar plates. These materials are typically obtained from various suppliers and undergo rigorous quality control measures to ensure their suitability for fuel cell production.
Catalyst Preparation:
The catalyst, commonly based on platinum, plays a crucial role in facilitating the electrochemical reactions within the fuel cell. The catalyst material is processed and prepared through various techniques, such as chemical deposition or physical vapor deposition, to create a highly active and stable catalyst layer. This layer is then applied to the electrode surfaces using methods like screen printing or spray coating.
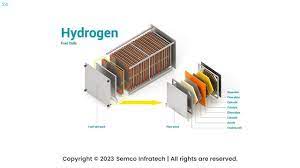
Membrane Electrode Assembly (MEA) Fabrication:
The membrane electrode assembly is a vital component of the fuel cell, comprising the polymer electrolyte membrane and the catalyst-coated electrodes. The polymer electrolyte membrane, often made of a perfluorosulfonic acid polymer, is carefully prepared and shaped to fit the fuel cell stack configuration. The catalyst-coated electrodes are then integrated onto each side of the membrane, forming the MEA.
Bipolar Plate Manufacturing:
Bipolar plates are responsible for distributing reactant gases and conducting current between individual fuel cells in a stack. These plates are typically made of lightweight and corrosion-resistant carbon-based materials. The manufacturing process involves molding, machining, or pressing techniques to create the desired shape and structure. Bipolar plates also incorporate channels and flow fields for the efficient flow of hydrogen and oxygen gases.
Fuel Cell Stack Assembly:
The fuel cell stack is the heart of the hydrogen fuel cell system, consisting of multiple fuel cells interconnected in series and parallel configurations. The MEAs, bipolar plates, and gas diffusion layers are precisely stacked together to create an assembly. Sealing materials, such as gaskets and adhesives, are used to ensure proper sealing and prevent gas leakage. The stack assembly is designed to maximize power output while maintaining optimal gas and coolant flow.
Balance of Plant Components:
In addition to the fuel cell stack, various balance of plant (BOP) components are required for a complete fuel cell system. These include hydrogen and oxygen supply systems, humidifiers, cooling systems, and power electronics for controlling and regulating the electrical output. The BOP components are integrated into the overall system design, ensuring proper fuel and coolant flow, thermal management, and electrical connectivity.
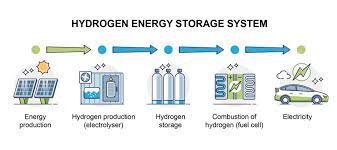
Quality Control and Testing:
Throughout the production process, rigorous quality control measures are implemented to ensure the reliability and performance of each fuel cell. Quality checks, including visual inspection, electrical testing, and performance evaluations, are conducted at various stages. Final fuel cell assemblies undergo comprehensive testing to verify their electrical output, efficiency, durability, and safety. Any defective cells or components are identified and replaced to meet the desired quality standards.
Deployment and Integration:
After successful production and testing, the fuel cells are ready for deployment and integration into various applications. This can include automotive vehicles, stationary power generation systems, or portable devices. The integration process involves connecting the fuel cell system to the necessary ancillary systems, such as hydrogen storage tanks, air intake systems, and power management units, to create a functional and efficient hydrogen-powered device.
Conclusion:
The production process of hydrogen fuel cells encompasses multiple stages, from raw material sourcing to the final integration of fuel cell systems. It involves the careful preparation of catalysts, fabrication of membrane electrode assemblies, manufacturing of bipolar plates, assembly of fuel cell stacks, integration of balance of plant components, and rigorous quality control and testing. This intricate process ensures the creation of reliable, efficient, and clean energy sources that have the potential to revolutionize transportation, power generation, and other industries. With ongoing research and development, the hydrogen fuel cell production process continues to evolve, driving the advancement of sustainable energy solutions.