Compared to batteries used in general applications, AGV lithium batteries need to possess characteristics such as fast charging, good stable performance, and safety. Conventional AGV vehicles operate as all-weather unmanned units, requiring sufficient energy to ensure long-term trolley operation. Lithium iron phosphate batteries are a more suitable choice due to their high safety, especially in fast charging environments. They offer safe and reliable performance along with a relatively stable discharge voltage platform.
In terms of battery volume and weight, there is a requirement for them to be small and light. AGV, as a handling tool, benefits from lighter lithium batteries as they reduce its burden. This allows AGV to complete tasks faster and with greater flexibility. Cylindrical lithium iron phosphate batteries, with their small volume and low capacity, are well-suited for matching the varying capacity and volume needs of AGV vehicles.
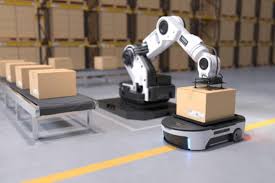
Long cycle life is a fundamental requirement. Presently, AGV trucks and forklifts have high overall costs, ranging from tens of thousands to hundreds of thousands. The high costs necessitate higher service life requirements for the entire vehicle. Customers always aim for long-term output with their investment. Among all mature secondary batteries, only lithium iron phosphate batteries offer a cycle life of more than 2000 times. From a long-term investment perspective, they are the most cost-effective option.
Communication is a necessary function of AGV lithium batteries, typically achieved using lithium-ion battery management systems (BMS) through RS485 or CAN communication modes. The purpose is to inform the AGV vehicle about the current status of the AGV lithium battery, enabling the vehicle to make informed operational decisions. However, ordinary lithium battery PACK manufacturers may lack BMS development capabilities, resulting in limited communication functions, SOC calculations, control modes, and other aspects. Therefore, attention should be given to the details during selection and screening.
Non-standard customization is the current status quo of AGV lithium batteries, as the market lacks a unified standard. Different models have varying power sizes, battery compartment designs, and functional requirements, leading to differences in battery size and other aspects. This necessitates supporting manufacturers to have sufficient design and development teams to meet the industry’s development demands. Traditional digital industry simple processing is no longer sufficient to address the industry’s evolving needs.