In this Article, we are discussing about Importance and function of Battery Management system how it works and protect the Battery.
Introduction
BMS is an electric vehicle battery management system, which is an important link between the vehicle power battery and the electric vehicle. The BMS collects, processes, and stores important information during the operation of the battery pack in real time, exchanges information with external devices such as the vehicle controller, and solves key issues, safety, usability, ease of use, and service life in the lithium battery system. The main function is to improve the utilization rate of the battery, prevent the battery from overcharging and over discharging, prolong the service life of the battery, and monitor the status of the battery. In layman’s terms, it is a system for managing, controlling and using battery packs.

1. What is a BMS system
1. The range of use of lithium-ion batteries is limited

For lithium-ion batteries, the ideal working range is very limited and not broad. Therefore, lithium-ion batteries must be managed during the application process, especially in the application scenario of power batteries.
2. Security Issues
- Distortion
- Swelling
- Flaming on fire
- Explosion



Overvoltage (overcharge), overcurrent and overtemperature will bring a series of safety hazards to lithium-ion batteries.
3. Performance Management
The external characteristics of lithium batteries are closely related to their own state (SOC/SOH/temperature) and ambient temperature.
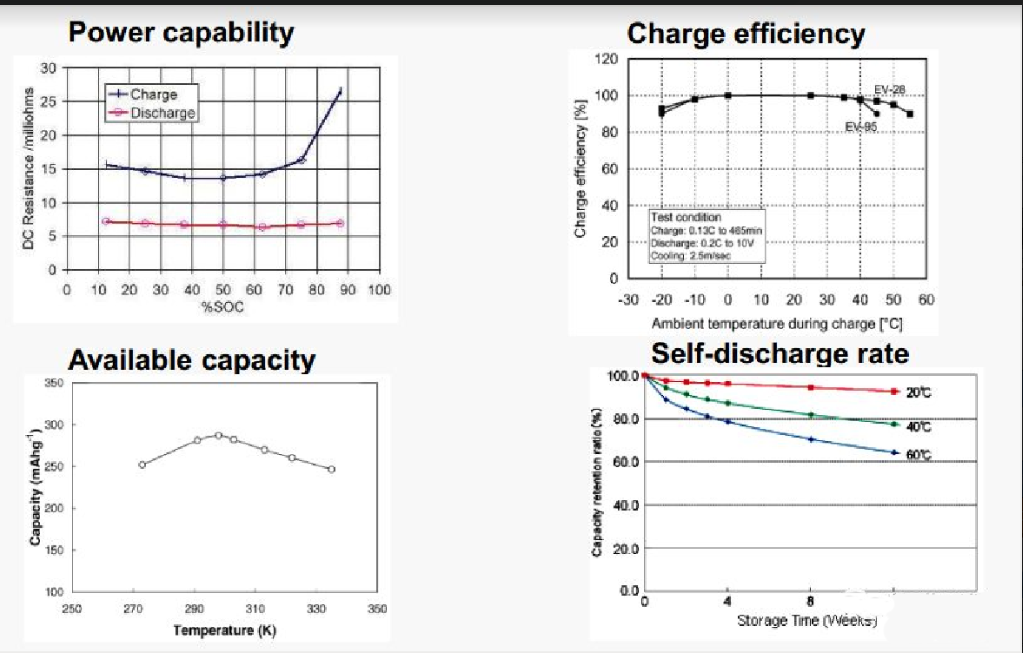
4. Longevity
- Temperature factor Environmental factor
- Voltage factor (SOC & ΔSOC) Voltage factor (SOC window)
- Current factor
High SOC and high temperature environment will aggravate the irreversible capacity loss of the battery
5. Consistency
- Capacity
- Impedance
- Self-discharge rate

It is almost impossible to require all the cells in the battery pack to be completely consistent, which means that there will be inconsistent working conditions (internal resistance / heat generation / SOC range) and different aging rates between the cells, so it is necessary to Balance management.
2. What is the Main Task of BMS?
Buy now – BMS Tester Machine
Main tasks of BMS:
- Battery status monitoring
- Battery status analysis
- Battery safety protection
- Energy control management
- Battery Information Management
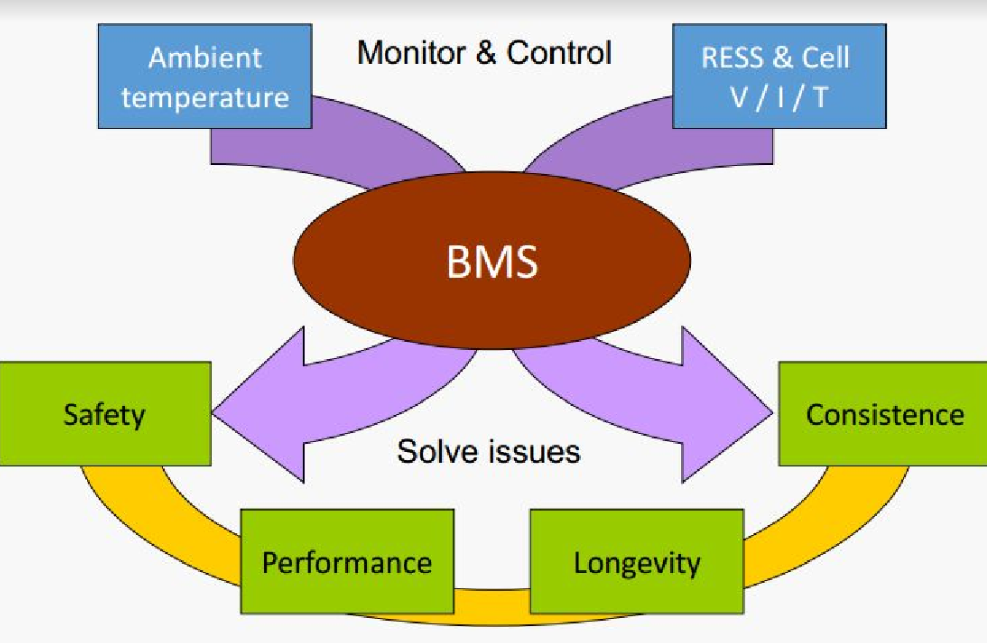
BMS needs to avoid over-range abuse of power batteries and ensure safe, reliable, efficient and long-life operation of power batteries.
3. Introduction to BMS System
1.1 BMS system architecture

A Typical BMS System Architecture

BMS System Architecture

Master-slave BMS topology
Local ECU layer
- Management of 6-12 cells in a module
- Communication via CAN or daisy-chain
- Voltage monitors for every cells
- Multi-points temperature monitor
- Passive balance or active balancing
- Function realization by MCU or ASIC
Is daisy-chained communication used?
Advantages
- No isolator for each LECU,
- Easy harness for system,
- Low cost,
Disadvantages
- EMI/EMC problem for vertical bus,
- Limited range,
- Break on daisy-chain cause the interruption of whole communication,

BMS Function List & Data Sampling Requirements
- BMS basic functions: V/I/T sampling, protection functions (overvoltage, overcurrent, overtemperature, insulation resistance), relay drive, status sampling, relay adhesion detection, CAN communication.
- BMS core functions: Cell balance, SOP (power), SOE (energy), SOC (state of charge), SOH (health level).
- BMS application related: Collision signal detection, AC/DC charging, charger status detection, thermal status, heating/cooling demand, pre-charging, wake- up/sleep, communication with VCU.
Buy Now: SEMCO Battery Management System Tester With Computer And Cabinet SI BMST 1 – 32S.
BMS Function List
Functional requirements | Comments |
Battery Pack high voltage sampling | Perquisites necessary to realize core functions. |
Battery pack current sampling | Perquisites necessary to realize core functions. |
Battery pack temperature sampling | Perquisites necessary to realize core functions. |
Cell voltage sampling | Perquisites necessary to realize core functions. |
Cell temperature sampling | Perquisites necessary to realize core functions. |
Over Voltage protection | RESS Basic security protection |
Over current protection | RESS basic security Protection |
Over Temperature protection | RESS basic security Protection |
Insulation Monitoring | HV RESS basic safety Protection |
Battery Equalization | Definition / Verification method @ implementation calculation activity |
ISOC Calculation | Verification Method / Implementation algorithm |
SOH Calculation | Define @ verification method / Implementation algorithm |
Static SOP Calculation | / Implementation algorithm |
Dynamic SOP Calculation | Verification method and |
Functional Requirements | Comment |
Can be done by VCU | |
Car Charging | Plug in model requirements |
Fast Change | Plug in model requirements |
Changing gun Condition monitoring | Plug in model requirements |
Thermal Status / Demand | Can be done by VCU |
Active cooling Control | Can be done by VCU |
Precharge | Depends on the architectural design |
Wake up/Sleep | Depends on the architectural design |
VCU Communication | |
Car Charger communication Fast | |
Charge communication | |
Troubleshooting | |
Software refresh and Calibration |
Estimating the remaining capacity of the Battery is the core content of the BMS and has always been a difficulty in the industry. First of all, it is an estimated value, which is calculated by the algorithm according to the battery pack voltage, current, discharge rate, temperature and other factors. This requires your system to collect accurate enough and fast enough to ensure the final result is accurate. But this is also related to the processing speed of your main control chip, the accuracy of the AFE, the selection of the current collection scheme, and the accuracy of the temperature sensor. There are also many factors related to the overall consideration of the sampling frequency of the system. Choosing a chip with high processing speed and high precision will inevitably increase the cost. The faster the sampling frequency, the greater the system load. Therefore, under the current technical conditions, everyone refers to their own specific projects to weigh various factors.

According to the V/I/T measurement value, estimate the internal resistance capacity and then estimate the SOC and SOH. The SOC and SOH are combined to obtain the SOP available power, which is finally reflected to the user as the remaining mileage.

Common industry requirements for estimation accuracy are as follows:

Data Sampling Requirements
- Data acquisition delay/synchronization issues
- BMS A/D conversion 100µs
- Communication network 2+8 bytes question and answer frame ~0.3ms
- BMS resource coordination and scheduling problems
- Fast charging safety issues
- Poor balance
- State Estimation Algorithm Accuracy Suggest
- Select sampling frequency according to signal characteristics (5~10 fmax)
- Different physical quantities, different sampling frequencies (I is the highest, T is the lowest)
- Information reporting requires systematic consideration to avoid false positives Data collection accuracy problem
- Current acquisition accuracy determines SOC accuracy
- Voltage accuracy affects SOC, safety
- Voltage accuracy determines the equalization effect Suggest
- Accuracy is not the higher the better
- Avoid high costs
- Over-reliance on accuracy reduces system reliability
- Appropriate precision, which needs to be fully demonstrated and verified
V/I/T Accuracy Requirements

The provisions in the national standard QCT897 are as follows: general enterprise standards will be higher than this,

Buy Now: SEMCO Battery Charge & Discharge Cabinet Tester SI BCDS 100V 10/20A 7CH.
Conclusion:
BMS helps in prevent battery failure and mitigate potential hazardous situations, which ensures that batteries function properly in the final application. It ensures that the battery operates efficiently, giving proper indications from time to time to the driver regarding the state and condition of the battery. It is the BMS that protects the battery from misuse and damage, prolongs battery life and ensures that the battery is always ready for use. In terms of the importance and safety of the car the BMS is definitely an underestimated part of the electric car and deserves the same attention as the battery itself.
More Articles:
BMS Battery Management System,
Battery Electrical Performance Test,
Safety Analysis of Li-Ion Battery,
IEC Battery Safety Standard for Power Batteries,
POWER BATTERY SHELL WATERPROOF DESIGN,
BATTERY SAFETY PERFORMANCE TEST,