In this Article, we are discussing different types of battery electrical performance test how batteries can be tested for performance.
INTRODUCTION
Batteries may be advertised as Long Life, High Capacity, High Energy, Deep Cycle, Heavy Duty, Fast Charge, Quick Charge, Ultra and other but advertising words can only mean whatever the Company wants them to mean. Apart from the basic battery design, performance actually depends on the environmental conditions of the battery under which they are used. Testing is designed to tell us things we want to know about individual cells and batteries.
The tests are usually carried out to verify that the cells meet the manufacturer’s specification but they could also be used to test the cells to arbitrary limits set by the applications engineer to determine how long the cells survive under adverse conditions or unusual loads, to determine failure modes or safety factors.
1. Battery Capacity
At a temperature of 23°C±2°C, Discharge with a constant current of 1C (if chemistry allows to the cut-off voltage and the released capacity is the rated capacity of the battery, which is often said to be battery capacity.
2. Nominal Voltage (Rated Voltage)
Also known as median voltage, it represents an approximation of the normal output voltage of a battery.
3. Charging Constant Current Ratio
When the battery is charged with constant current and constant voltage to the final voltage, the ratio of the capacity charged by constant current to the total capacity charged gives Charging constant current ratio.
The ratio of constant current = Constant current charging capacity/ (Constant current charging capacity * Constant pressure charging capacity) * 100%.
4. The Magnification Test
4.1 Rate charging test
- First Discharge Battery with 1C current, then with 1C current charging,
- Calculation 1C charge capacity/Initial capacity*100%Battery with 1C After the current is discharged, then with 3Ccurrent charging, calculation 3Ccharge capacity/Initial capacity*100%
- Battery with1C After the current is discharged, then with 5C current charging, calculation 5C charge capacity/Initial capacity*100%
4.2 Rate discharge test
- Battery with 1C After charging with current, then with 1C current discharge, calculation 1C put in capacity/Initial capacity*100%,
- Battery with 1C After charging with current, then with 3C current discharge, calculation 3C put in capacity/Initial capacity*100%,
- Battery with 1C After charging with current, then with 5C current discharge, calculation 5C put in capacity/Initial capacity*100%,
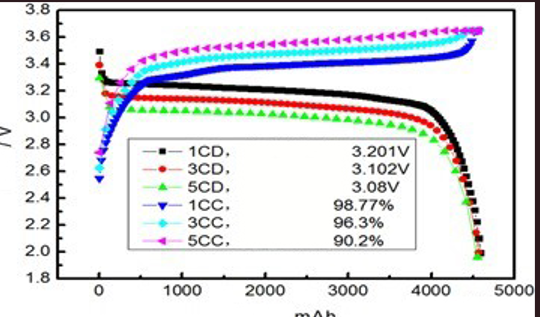
5. Low Temperature Performance Test (High Temperature Performance Test)
By using 1C Charging, Charge the battery with constant current and constant voltage to the final voltage, and then put the battery in a low temperature-10°C, -20℃ or-40℃ applicable for 30min-60min, then use 1C current discharges up to the cut-off voltage,
Calculate the low temperature discharge rate = 1C Discharge capacity/initial capacity*100%.
6. Capacity Retention Test
Generally, after the battery is fully charged, leave it at room temperature or high temperature for a period of time, and then use 1C Current discharge,
Calculation of Capacity retention = 1C Discharge capacity/initial capacity*100%
7. Capacity Recovery Capability
Capacity recovery is also known as charge recovery capability. The test method is to store the battery for a period of time at room temperature or 1C current discharge, and then proceed 1C current charge and finally, 1C current to discharge, and Compute,
Capacity resiliency = final discharge capacity/initial capacity * 100%
8. Cycle Test
Battery with nC current for constant current and constant voltage charge and then nC current for discharge, gives cycle times until the capacity is the initial capacity 80% of original.
Note: At present, there are also applied power cycles, which are more in line with the conditions of use. Electric tools are generally charged and discharged with constant power.
9. Voltage Self-Discharge Test (K value)
Adjust the battery voltage to a certain process value, place it at the set temperature for t hours or days, and continuously test the battery voltage change.
K= (Vt-V0)/ tin
Vt is the final test voltage value And V0 is the initial voltage value for time.
Two parts of battery safety performance test items
*Illustrate:
①1C rate: If the battery capacity is 5Ah, 1C means the current is 5A, and 2C means the current is 10A.
②C5: refers to a 5-hour rate, equivalent to 0.2C current for discharge
Buy Now: SEMCO Battery Charge & Discharge Cabinet Tester SI BCDS 99V – 20A – 1CH.
1. Overcharge Test,
1. Use as required 1C current to fully charge the battery,
2. Then continue to use 1C Current for constant current charge to the battery terminal voltage up to 1.5times of full charge voltage,
3. Observe 1h
2. Over Discharge Test,
1. Use as required 1C current fully charged,
2. Then use1Ccurrent discharge90min,
3. Observe 1h
Buy Now: SEMCO Battery Charge & Discharge Cabinet Tester SI BCDS 100V 10/20A 7CH.
3. Reverse Charging (Forced Discharge)
1. UN 38.3 Standard forced discharge: connect batteries in series to 12V in the DC power supply, discharge is carried out according to the specified current and time,
2. GB 31241 Standard forced discharge: use 1C reverse current charging 90min.
4. Short Circuit Test
1. Use 1C current to fully charge the battery,
2. Reuse resistance ≤5m Ω wire to shorts the positive and negative poles of the battery,
3. Observe 1h
5. Incineration Test
Batteries are placed in each inch (25.4mm).
1. The wire mesh is placed at a distance from the burner at 1.5-inch (38.1mm) distance.
2. Fuel and air are jetted at speeds that provide a bright blue flame, so that the wire mesh burns bright red.
3. 1 denim panel placed at 3 feet perpendicular to the centre of the steel network (0.91m) location. The denim sheets for a yard Fang, consists of four layers per square yard 0.4-0.6 Constructed of ounce heavy denim material.
4. It should be required to circle the experimental sample in the net, then ignite the burner and observe the battery until it explodes or is destroyed.

6. Acupuncture Test
1. Use 1C current to fully charge the battery,
2. With Φ5mm-Φ8mm High temperature resistant steel needle, with25±5mm/s , The speed runs through the vertical direction of the battery,
3. Observe 1h

7. Drop Test
1. Use 1C current to fully charge the battery,
2. Battery positive and negative terminals from1.5m height, fall to the mud,
3. Observe 1h

8. Extrusion Test
1. Use 1C current to fully charge the battery,
2. with radius 75mm Half-cylinder, the length is longer than the battery length, the speed 5±1mm/s,
3. Voltage reaches 0V or the deformation amount reaches 30% or the extrusion force reaches200KNstop test,
4. Observe 1h

9. Heating Test
1. Use 1C current to fully charge the battery,
2. Discharge the battery in the thermostat, the thermostat follows the 5°C/minaret up to 130°C±2°C, Keep 30min,
3. Observe1h
CONCLUSION
The battery can provide energy for electric vehicles and increase the power for electric vehicles. This is the reason that electric vehicle manufacturers, and maintenance plants to have a deeper understanding of the performance of electric test. This is not only to extend the battery life of electric vehicles, but also to speed up the work and improve the efficiency of the work by the driver or the repair shop as soon as the accident occurs. The focus of this article is to explain the methods and precautions for testing the electric vehicle system with the performance of the power battery, and strive to play a positive role in the development of the power battery of the electric vehicle.
More Articles:
BMS Battery Management System,
Battery Electrical Performance Test,
Safety Analysis of Li-Ion Battery,
IEC Battery Safety Standard for Power Batteries,
POWER BATTERY SHELL WATERPROOF DESIGN,
BATTERY SAFETY PERFORMANCE TEST,