Introduction
Everything we do has a program, a process. The same is true for electric vehicle maintenance. When repairing vehicles, you must have a way of thinking and a complete process for each faulty car.
We received the faulty car, and the first thing we must do is to ask about the fault phenomenon of the vehicle and record the fault phenomenon for analysis. There will be many failures in electric vehicles failures, such as battery failure, constant power of controllers, non-powering headlights, etc., but no matter the size and number of the failures, they can be grouped into two categories:
1. Flexible failure
The so-called flexible failure refers to the failure that occurs and sometimes disappears. Or there is no obvious law to follow when a fault occurs. For example, the copper wire in the controller is de-welded, sometimes it has good contact and the motor runs normally; sometimes if the contact is not good, the motor will start weakly. Such failures must first analyze the relevant aspects and measure the relevant parameters. If there is no clue for a while, the simplest and most effective way is to replace the parts.
2. Rigid failure:
The so-called rigid fault means that once such failures occur, they will always exist, the scope of failures will not be expanded, the faults will not be transferred, and the fault phenomenon will not change. If the power brake handle is damaged, it is impossible to cut off the motor power supply. Just replace it with a new product. This kind of fault is easier to repair. Generally, those who know a little theoretical know l edge can judge first and then replace the parts to improve the maintenance rate.
We also have a principle of repair – minimize failure. Simple problems themselves have been minimized, and complex problems should grasp the key points of the problem and find a breakthrough to solve.
There are many parts to electric vehicles. The maintenance of electric vehicles is essentially the maintenance and replacement of parts, so let’s follow the Adige to learn about the possible failures of electric vehicles from the key 11 parts.
Buy Now: Semco Infratech – SI Battery Charge & Discharge Cabinet Tester – SI BCDS 100V 20A 4CH.
1. Frame
The frame is the safety core of the whole vehicle, and poor frame strength or production accuracy will seriously affect its use.
● If it is found that the whole car is always tilted to one side when riding, it may be that the whole vehicle is tilted;
● If the whole car has a serious concave, it may be overloaded and rode in poor road conditions, resulting in deformation of the whole vehicle. The possibility of deformation is a crack in the front riser and the front triangle welding or a crack in the joint of the saddle pipe flat fork and the frame;
● If there is a “clicking” metal knocking sound, it should be a problem with the strength or welding of some joints.
2. Backplate Fork
There is generally no big problem with the rear fork, mainly because the rear fork screws are loose during installation or in poor driving conditions. Once the rear fork screws are loosened, the rear wheel swings will occur, resulting in a serious swing of the tail when braking. The vehicle will shake when riding at high speed, and the chain may fall off when the pedal is pedaled. The strength of the motor joint on the rear fork is also very important, especially the size and rigidity of the opening, because in emergency situations (such as emergency braking), it is a great test of rigidity, so the operation that can be returned half a lap is usually done after tightening the nut of the motor, which will not easy to loosen.
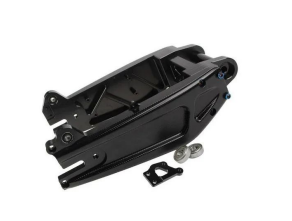
3. Fork
The fork is divided into simple shock absorbers. Nowadays, electric vehicles generally use shock absorbers. The fork is relatively easy to damage. General collisions and powerful dives will damage the fork springs. The result of damage is that the front wheel mud plates with the front triangle or the front wheels and plastic parts, resulting in vehicles not being able to turn. When this happens, we can use greater force to press the front fork to see whether to replace the fork or use another method to increase the gap of the fork.
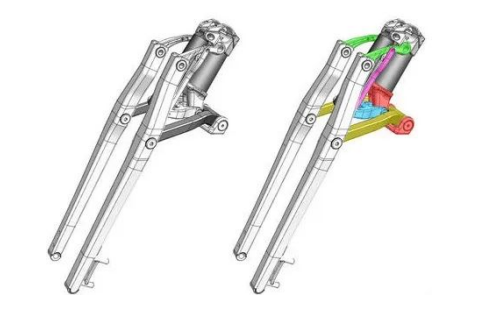
4. Handle Riser
Generally, there is nothing wrong with the handle and riser in a new car, but it may rust after a long time. At this time, we can’t force the screw screws. We should first treat it with rust water for a period of time, and then carefully knock on the outside of the front riser with an iron hammer. We’d better use a plum board hand or sleeve when screwing the screw. The barrel wrench is generally not a rigid hand or a live wrench.
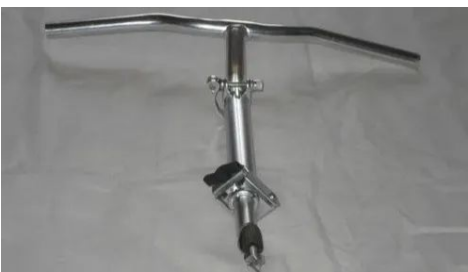
6. Plastic Part
Plastic parts are generally not repaired. This article mainly wants to talk about the resonance problem of plastic parts. When there is a resonance problem, we mainly consider whether the fasteners are loose. If necessary, we can add a stick to the plastic part to change the frequency of the resonance for repair.
7. Instrumentation
Instruments are the display parts of electric vehicles. Nowadays, the instruments commonly used are divided into LED displays and pointer displays. The failure rate of LED instruments is generally relatively low, but once there is a fault, it is difficult to check. We must understand the characteristics of some comparators, the structure of the voltage regulator circuit, etc. If the voltage indicator is inaccurate, the adjustable resistance of the benchmark can be adjusted to achieve it.

When designing LED instruments, it is very likely to focus some auxiliary functions (such as Undervoltage indication, caller ID, cruise, etc.) on the dashboard, so we must understand the functions of the circuit board before repairing. Pointer instruments can be divided into brushed and brushless according to the speedometer and can be divided into positive control and negative control according to control polarity.
9. Cable
The essential damage to the cable is not easy to touch in the repair, but it is time-consuming and laborious to find the cause. Generally, when working, first look for the area where the problem may occur according to the functions of the controller or display, and then find the connection of the cable according to the corresponding colour.
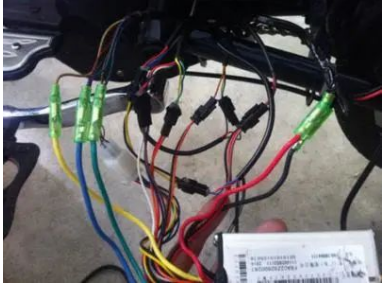
8. Controller
Controllers are one of the most concerning devices in repair, and damage to controllers is also more common. Generally, the controller lead includes several items: power cord, motor wire, brushless, generally five-core Hall wire, brake handle wire, speed line, brake light wire, Undervoltage wire, power line, etc. From the appearance, the thicker wire diameter (more than 1.5mm) is the power cord and the motor line, the five-core bundle is generally the motor Hall signal line, the rotary brake handle wire is generally a three-core 2 or four-core 1 plug-in, and the speed line, brake light wire and Undervoltage wire are generally single-core wire;
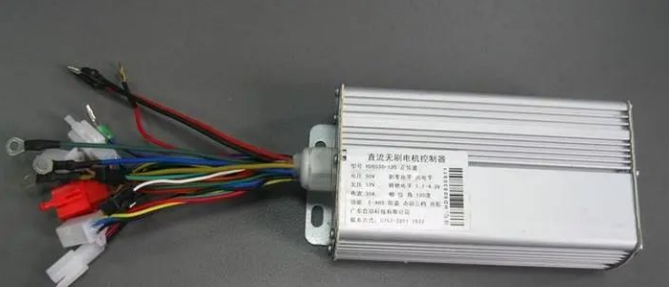
If you want to verify whether it is correct, just rotate the handle to detect whether the signal voltage is 0.8-4.2V (5V power supply); the brake has two wires (mechanical switches) and three wires (Hall switches), and the two-wire mechanical switches can only close and disconnect, and the Hall brake of three lines. Like the turn shift, judge the power supply first, and then judge the signal. Generally, there are two kinds of brakes: normal height and normal low. When the normal height brake action, the signal is to the ground, and the normally low brake handle is exactly the opposite.

The speed line, brake light line, Undervoltage line, and power line are generally measured by measuring the ground voltage during the corresponding action. Generally, the damage to the controller is characterized by the motor not turning, the loud rotation noise, the rotation, the reversal of the forward rotation, the fast temperature of the controller, the weakness of the motor, etc.
9. Motor
Motors used on the market generally have to brush low speed, brush high speed, brushless low speed, etc. Brushless high speed is generally not commonly used. The difference between high speed and low speed mainly lies in whether the gear deceleration is. The purpose of gear deceleration is to improve the speed of the motor, thus improving the efficiency of the motor at low speed and increasing the output torque at low speed. We mainly judge the performance of the motor with the following indicators:
● Motor noise. Noise is available in each motor, but there can be no noise of metal collision, marble extrusion, and friction, allowing uniform electromagnetic noise, which can be monitored on the motor shaft through hollow metal listening rods.
● Motor is on-board current. The detection of the no-load current of the motor mainly reflects the demagnetization of the motor and the wear loss of the machinery. If the current increases and the no-load speed of the motor increases, it generally shows that the demagnetization phenomenon is obvious.
● Motor load current. Detecting the load current of the motor mainly reflects the actual operating efficiency of the motor. If the load current increases, but the actual torque is small, it means that the efficiency of the motor is very low. It is necessary to check the magnetic energy volume of the magnetic steel. In addition, the welding inside the coil should also be paid attention to. If there is a brush motor, it is necessary to check whether the commutator has a short circuit. Phenomenon
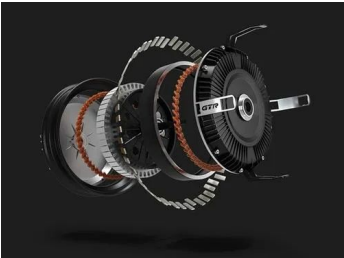
Buy Now: Semco Infratech – SI Battery Management System Tester – SI BMST 1-32S 60/120A with cabinet.
10. Battery
Nowadays, electric vehicles generally use lead-acid batteries. The regular detection of lead-acid batteries must detect the actual capacity. Generally, 0.5C is the standard discharge, and C is the capacity value of the 2h rate. If the capacity value specified by the manufacturer is not reached, it can be replaced during the repair period. During service, it can be simply detected in the following ways:
● Measure the end voltage of the battery and test the short-circuit current of the battery. If the end voltage of the battery is high, but the spark is very small in the short circuit, it means that the battery has open circuits and other situations. Generally, there are relatively few welding fractures of the internal electrodes. Pay attention to checking the virtual welding of exposed terminals and the serious corrosion of the electrodes.
● Immediately after being fully charged, measure the battery end voltage, then place it for more than 5 hours, and detect the end voltage again. If the voltage drops greatly, and it still drops to a large extent during the re-measurement process, it means that the battery self-discharge is very serious and generally needs to be replaced.
● During the charging process, the battery is seriously hot, but the battery has not been deformed, you need to check the charging current of the charger. Generally, the charging current of the 10- 14Ah battery is about 1.6-1.8A, and the charging current above 17Ah-20Ah is about 2.5-3.0A. For batteries, moisture is lost due to severe heat, so it is necessary to replenish moisture.

The simple operation is as follows: open the cover of the battery, rotate down the battery’s 6 safety valves, add pure water or distilled water to each grid of about 6mL, and use a pulse charger to charge deeply, discharge at 0.5C, and cycle again, which should be greatly improved.
When we detect the battery voltage of electric vehicles, we can choose the battery quick judgment. This article wants to say that this instrument is really cost-effective! A meal is exchanged for free testing~
They can judge the quality of a single battery by the voltage difference between the open circuit voltage and the discharge cut-off voltage, and can also record the voltage difference of each battery in the whole set of batteries to judge the balance of the whole battery. The parameters of the LED display are clear at a glance and are one of the indispensable and important tools for repairers
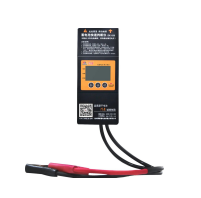
The three-stage charger mainly detects the following items:
● Output of empty load voltage. This value generally indicates whether the switching power supply is working properly.
● The instructions for the charger are correct. Generally, it is charged in red and filled with green.

● Whether the charging current of the charger is correct. The charging current of the charger is explained in the battery and will not be repeated here.
● Charging current after 6-8 hours. Generally, the three-stage charger will be recharged after 6-8h. If it cannot be converted to a floating charge, the charging current is still large, causing the battery to heat up, so it is necessary to check the battery to detect the battery’s charge when the charging current is less than 450mA (10-14Ah) or 650mA (17-22Ah). Whether the pressure is under the floating charging pressure.
● If it is a pulse charger, you still need to check the pulse current. The simpler way is to see whether the ammeter serial into the battery has a regular litter.
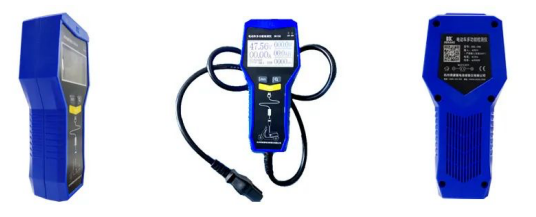
Conclusion
When we detect electric vehicle chargers, we can also choose an electric vehicle multi-function tester, which can detect chargers, motors, and battery solar photovoltaic panels. And it has functions such as maintaining and extending battery life, which can definitely meet your requirements. And the cost performance is super high.
More Articles:
Principles of Power Battery Cooling System,
How Many Degrees Of Electricity Does An Electric Car Need To Be Filled At A Time,
Battery Repair System Product Description And Overview,
Analysis of Common Terms for Lithium Batteries,
Charging & Maintenance Methods for Nickel-Hydrogen Batteries,
Common Failure Modes & Causes of Electric Vehicle Batteries,
Can Lithium Batteries in Electric Vehicles be Charged Quickly,
Best Time to Charge Electric Vehicle Battery,
Causes of Battery Failure in Electric Vehicles,
Pre-Lithiation Strategies for Lithium Battery,
Latest Technology of Lithium Battery,