Introduction
In the fast-evolving landscape of battery production, manufacturers are constantly seeking advanced technologies to enhance efficiency, precision, and cost-effectiveness. Battery laser welding machines have emerged as a revolutionary solution, offering a wide array of benefits that cater to the demands of modern energy storage systems. This article explores the various advantages of employing battery laser welding machines in the manufacturing industry, highlighting their role in revolutionizing battery production processes.
Unparalleled Precision
Precision is a crucial factor in battery production, where even the tiniest defect can significantly impact performance and safety. Battery laser welding machines provide unparalleled precision, thanks to the focused and concentrated beam of the laser. This allows for extremely fine and accurate welds, ensuring the integrity of delicate battery components, such as thin foils and electrodes. As a result, manufacturers can consistently produce high-quality batteries with minimal defects, improving overall reliability and customer satisfaction.
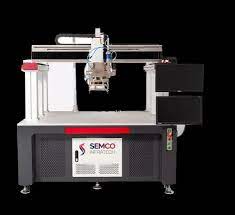
Enhanced Efficiency
Efficiency is a key driver in any manufacturing process, and battery laser welding machines excel in this regard. Their high welding speeds and rapid heat input minimize production cycle times, enabling faster throughput and increased productivity. Additionally, the non-contact nature of laser welding eliminates the need for consumables, reducing downtime for material changes and reducing overall maintenance costs. This efficiency translates into greater output, making laser welding an indispensable technology in meeting the rising global demand for energy storage solutions.
Reduced Production Costs
In the competitive manufacturing landscape, cost optimization is a paramount concern. Battery laser welding machines contribute to cost reduction in multiple ways. Firstly, their precision minimizes material wastage, resulting in fewer rejected components and lower scrap rates. Secondly, the high automation potential of laser welding allows for streamlined workflows, reducing the need for manual labor and associated labor costs. Furthermore, the speed and accuracy of laser welding lead to fewer rework cycles, saving time and resources. Over time, these cost-cutting benefits make battery laser welding a financially viable option for large-scale production.
Versatility in Battery Design
Battery designs have become increasingly intricate to cater to diverse applications, from portable electronics to electric vehicles and renewable energy storage. Battery laser welding machines offer unparalleled versatility in welding complex geometries and dissimilar materials. They can handle a wide range of battery cell formats, from cylindrical and prismatic to pouch cells, facilitating the production of custom battery packs tailored to specific applications. This adaptability grants manufacturers the flexibility to stay at the forefront of innovation and adapt to rapidly evolving market demands.
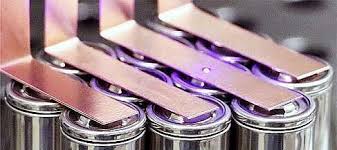
Minimal Heat-Affected Zones
Traditional welding techniques can introduce significant heat into the weld area, potentially causing thermal stress and affecting battery performance and longevity. In contrast, battery laser welding machines generate minimal heat-affected zones (HAZ) due to their focused and precise energy delivery. This characteristic reduces the risk of damage to temperature-sensitive battery components and preserves the material properties, ensuring the highest level of performance and safety.
Improved Safety Standards
Battery safety is of utmost importance, especially in high-energy applications like electric vehicles and energy storage systems. Battery laser welding machines play a vital role in enhancing safety standards by producing strong and reliable welds. The integrity of laser-welded joints reduces the risk of battery leakages, ensuring that batteries can withstand challenging operating conditions without compromising safety.
Environmental Friendliness
In today’s environmentally conscious world, sustainable manufacturing practices are a priority. Battery laser welding machines contribute to eco-friendly production processes in several ways. Their high efficiency and precision result in less material waste, reducing the environmental impact of manufacturing. Additionally, the non-contact nature of laser welding means no fumes or harmful byproducts are emitted during the welding process, creating a cleaner working environment and contributing to a greener manufacturing facility.
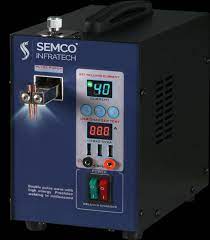
Conclusion
The advantages of battery laser welding machines in the manufacturing industry are undeniable. Their precision, efficiency, and ability to reduce production costs make them a game-changer in battery production processes. As energy storage technology continues to advance, battery laser welding machines will play a pivotal role in shaping the future of battery manufacturing, enabling the development of safer, more efficient, and environmentally friendly energy storage solutions. With ongoing research and development, it is certain that these machines will continue to evolve, empowering manufacturers to meet the growing demands of the global energy landscape.