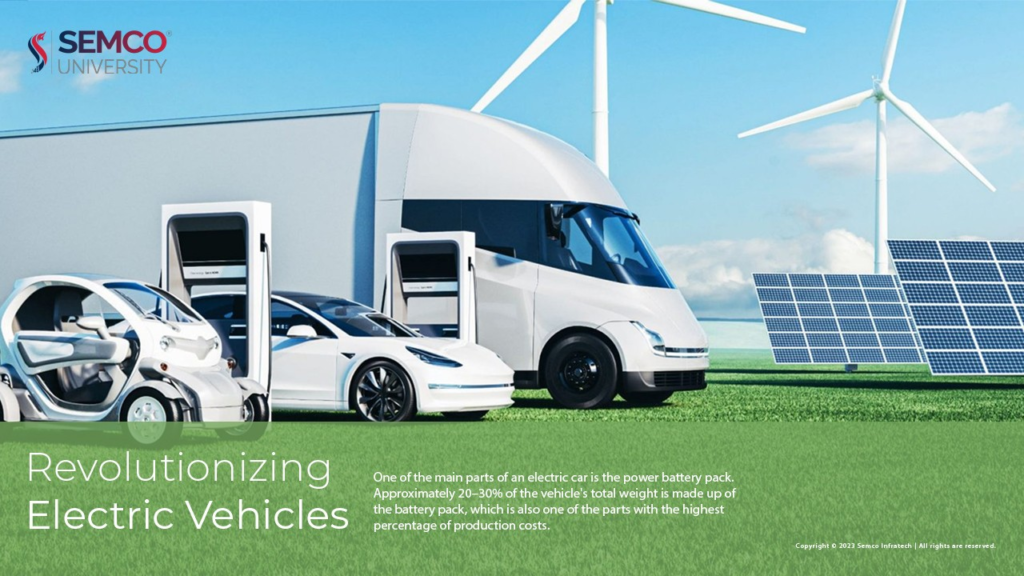
One of the main parts of an electric car is the power battery pack. Approximately 20–30 percent of the vehicle’s total weight is made up of the battery pack, which is also one of the parts with the highest percentage of production costs.
As everyone is aware, the battery pack’s safety specifications are very stringent, and they also affect the vehicle’s overall power and range performance.
The overall weight of the car body is also important to improve performance. Among these, the battery packs’ lightweight—which makes up almost one-third of the total weight—has also emerged as crucial.
What makes the battery pack so light?
Traditional fuel vehicles can increase their efficiency by 6-8% and reduce their weight by 10 percent, according to research data. Electric vehicles can have their weight reduced by 10 percent while driving at a constant speed, which can result in a 10% increase in the vehicle’s overall driving mileage.
So how can the range be improved?
From the standpoint of battery packs, you can only begin weight loss at the structural level because of the significant restrictions on the size and composition of cell materials. Companies that manufacture new energy vehicles are now concentrating their research on lightweight boxes and modular compacting.

How to create a battery pack that is lightweight?
There are two main levels of the battery pack’s lightweight: the system design level and the detailed design level.
The battery pack’s construction still has to adhere to fire safety regulations, sealing insulation requirements, and mechanical safety requirements in addition to being lightweight. The battery pack’s performance is dependent on the box structure’s strength, stiffness, stability, and resistance to collisions.
The following five techniques are the most successful in the lightweighting journey:
Optimize the battery pack arrangement
A specific number of battery cells form modules within the constrained battery box through mechanical and electrical connections. These modules are arranged in series and parallel based on the spatial shape and bearing characteristics of the vehicle battery pack, with diverse layouts and structures. Battery monomers, including soft-coated aluminum plastic film, square aluminum shell, and cylindrical types, are common, accompanied by auxiliary components like a high-voltage wire harness and a BMS controller. The power battery pack’s layout is influenced by the car’s space characteristics, driving mode, center of gravity, and ground clearance. Manufacturers adapt module layouts, battery box shapes, and lug positions to meet the specific requirements of vehicle enterprises, resulting in common structural layouts like body bottom suspension, body structure integrated, and standard box distribution.
- Suspension at the body’s base
The majority of early electric cars were converted from conventional fuel cars. Power battery packs are typically mounted in the car’s floor, trunk, front compartment, and other locations.
The bottom of the car frame is bolted to the suspension battery pack located at the bottom of the body, offering good production and manufacturing independence along with an efficient and adaptable design.
- Distribution of boxes
Multiple standard box battery packs connected in parallel form the distribution of standard boxes, which has the advantages of a flexible layout and a variety of installation locations.
Large and regular passenger cars or special vehicles with large spaces mostly adopt this structural form.
- Integrated body structure
The traditional vehicle structure, which has limited space, is unable to meet the optimal design requirements due to the increasing demand for electric vehicles with longer ranges. As a result, the layout of the integrated battery package structure of the body structure has gradually received attention.
A unique design platform for electric vehicles has emerged as a result of the advancement of electric vehicle forward design technology.
The growing need for electric vehicle range combined with the advancement of automotive design technology has encouraged cooperation in the development of body style and battery pack architecture, with the goal of achieving a small body size and superior battery pack efficiency. The number of platform-based and modular body structure integrated power battery packs is currently steadily rising.
Upgrade the battery modules
The choice of cell parameters and monomer size is the first step towards the lightweight design of the battery pack at the system design level.
Lithium-ion power cells and power battery systems have complementary design issues with respect to various chemical systems and size parameters. These issues are typically calculated and determined during the conceptual design phase of the battery system.
Lastly, by lowering the design level and refining the internal battery box layout, the maximum utilization rate of the box space is achieved.
The battery cell is integrated into the upper and lower shells of the battery package and the shell is filled with thermally conductive glue. The monomer and battery management system are fixed directly into the battery package shell.
Furthermore, a pressure or temperature sensor is integrated into the cell shell, situated between the cell’s side wall. When the two sensors work together, it is possible to identify the faulty cell unit and prevent safety incidents like thermal runaway.
The absence of a module structure increases the battery pack’s volume utilization rate by 15% to 20%. Assembling each cell separately lowers assembly complexity and boosts production efficiency by roughly 50%. More significantly, though, is the ability to identify and replace defective cells on time and lower the level of protection the battery pack shell receives thanks to the cell shell strengthening scheme.
New grouping method
- Large module design
Increase the size and capacity of the single cell, resulting in the reduction of the quality of the structural parts shared by each single cell. It is reported that this design can increase the battery pack by about 50% and reduce the production cost by about 30%.
Application of lightweight materials
The incorporation of lightweight materials, such as aluminum-magnesium alloys and composite materials, in electric vehicle design, notably the battery pack, plays a pivotal role in the pursuit of enhanced efficiency and performance.
While aluminum alloy stands out for its lightweight and recyclable properties, composite materials offer extreme lightness, insulation, and simplified processing, replacing traditional metal parts in various vehicle components. However, challenges like raw material limitations and cost considerations persist.
Innovations include the application of sandwich structures and the integration of metal or honeycomb aluminum structures to balance weight, strength, and collision resistance. Despite their weight reduction benefits, current research lacks comprehensive design methods for battery pack structures that excel in both performance and weight reduction, emphasizing the ongoing need for advancements in multi-material design methods for electric vehicle components.
Extreme design
Extreme design typically investigates the performance thresholds and parameters of a product’s production process and precisely locates them.
For instance, the load-bearing portion of the battery box’s design is strengthened, rather than employing materials with thin walls. To achieve structural performance, satisfy design specifications, and minimize weight, the box’s thickness varies at different points.
The pursuit of lightweight power battery packs is driving innovation in electric vehicle technology. As new methodologies and materials continue to emerge, the quest for an optimal balance between performance, safety, and weight reduction remains at the forefront of electric vehicle development.
__________________________________________________________________________________________________________________________________________________
About Semco – Semco University is an educational website that is catering to the needs of students and researchers. Offering information on Lithium-ion batteries. The resources and content are compiled from various sources including manufacturers, test labs, crowdsourcing, etc. Our motto is to provide a viable resource for companies, students, and enthusiasts interested in participating in the Li-ion Battery industry. Our initiative is to make people aware of the benefits, and opportunities of the revolutionary Lithium Batteries for multiple applications.
For More Updates Follow Us
WhatsApp – Facebook – Instagram – Twitter – LinkedIn – YouTube