Lithium-ion battery PACK technology is an important part of the skills of the energy storage industry. Let’s learn some basic knowledge of battery PACK.
Definition
Lithium-ion battery PACK, also known as battery module, is a production process of lithium-ion batteries, which means packaging, packaging and assembly. It refers to the connection of multiple lithium-ion monomer cell groups in series, and considers the mechanical strength of the system, thermal management, BMS matching and other problems. Its important technology is reflected in the overall structure design, welding and processing process control, protection level, active thermal management system, etc. If two batteries are connected in series or in parallel to form a specific shape according to the customer’s requirements, it is called PACK.
Composition of battery PACK
The important components of battery PACK include single battery module, electrical system, thermal management system, box and BMS.
Battery module: If the battery PACK is compared to a human body, then the module is the “heart” responsible for the storage and release of electrical energy.
Electrical system: It is mainly composed of connecting copper sheets, high-voltage wire harnesses, low-voltage wire harnesses and electrical guarantee devices.
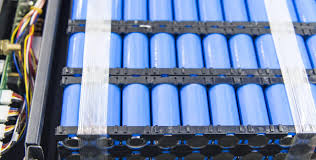
The high-voltage wire harness can be regarded as the “aorta blood vessel” of the battery PACK, which continuously transmits the battery power to the terminal load, while the low-voltage wire harness can be regarded as the “neural network” of the battery PACK, which transmits detection signals and control signals in real time.
Thermal management system: The thermal management system mainly includes air cooling and liquid cooling, while liquid cooling can be divided into cold plate liquid cooling and immersed liquid cooling. The thermal management system is equivalent to installing an air conditioner for the battery PACK.
The battery will generate heat in discharge mode. In order to ensure that the battery works at a reasonable ambient temperature and improve the cycle life of the battery, the system temperature difference is generally required to ≤ 5℃.
Box body: It is mainly composed of box body, box cover plate, metal bracket, panel and fixing screw. It can be regarded as the “skeleton” of the battery PACK, which plays the role of supporting, resisting mechanical shock, mechanical vibration and environmental protection.
BMS: Battery management system The battery management system can be regarded as the “brain” of the battery. It is mainly responsible for measuring the voltage, current, temperature and other parameters of the battery, as well as equalization and other functions. Data can be transmitted to MES.
Features of battery PACK
PACK lithium battery pack requires a high degree of consistency (capacity, internal resistance, voltage, discharge curve, life).
The cycle life of the battery pack PACK is lower than that of a single battery.
Use under limited conditions (including charging, discharge current, charging mode, temperature, etc.)
After the lithium battery pack PACK is formed, the battery voltage and capacity are greatly improved, which must be protected for charging equalization, temperature, voltage and overcurrent monitoring.
The battery PACK must meet the voltage and capacity requirements required by the design.
The method of PACK
Consists of series: The battery module is made of single cells connected in series. The capacity is increased in parallel, and the voltage remains unchanged. After series, the voltage is doubled and the capacity remains unchanged.
For example, a cell with a voltage of 3.2V, 15 cells connected in series is 48V, which is series boost.
For example, a cell with a capacity of 50Ah, two connected in parallel, will have 100Ah, which is parallel expansion.
Cell requirements: Select the corresponding cell according to your own design requirements. The battery requirements for parallel connection and series are the same type and model, and the difference in capacity, internal resistance and voltage value is not more than 2%. Whether it is a soft-wrapped battery or a cylindrical battery, it needs multiple combinations.
PACK process: The PACK of the battery is realized in two ways. One is through laser welding or ultrasonic welding or pulse welding, which is a common welding Project name Parameter indicators method. The advantage is that it is reliable but not easy to replace.
The second is contact through elastic metal sheets. The advantage is that there is no need for welding, the battery replacement is easy, and the disadvantage is that it may lead to poor contact. Considering the yield, efficiency and internal resistance of the connection point, laser welding has become the first choice for many battery manufacturers.